Industria auto traversează un amplu proces de tranziție spre mașini electrice pentru a reduce impactul asupra mediului înconjurător, iar acest lucru are efecte inclusiv în ceea ce privește operarea uzinelor de producție.
De exemplu, Grupul BMW a anunțat în acest an o nouă abordare sub numele BMW iFactory, prin care a stabilit o serie de măsuri care vor fi implementate treptat în toate uzinele. Noua abordare iFactory presupune o mai mare eficiență în cadrul procesului de producție, utilizarea unor materii prime și surse de energie prietenoase cu mediul înconjurător și utilizarea activă a tehnologiilor digitale, inclusiv inteligența artificială.
Pentru a vedea modul în care se adaptează BMW la noul concept, am vizitat recent două uzine din Germania ale Grupului, una inaugurată în 2020, iar cealaltă în 1973.
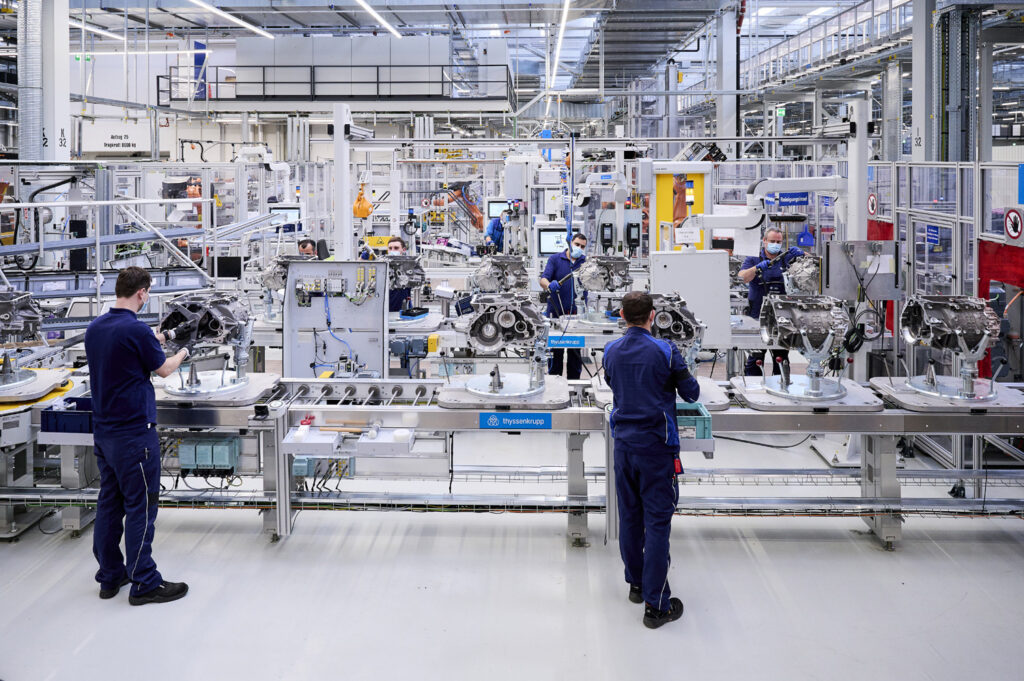
Additive Manufacturing Campus
Intrăm pe străduțele din Oberschleißheim, o municipalitate din districtul Munchen situată la numai 13 kilometri nord de centrul orașului, în care locuiesc circa 12.000 de locuitori. Pare un orășel liniștit tipic german și absolut nimic nu ne pregătește pentru ceea ce avea să urmeze. Nici măcar atunci când intrăm în parcare.
“Seamănă cu un banal showroom BMW”, îmi spun în gând. Senzația asta rămâne și după ce intrăm în clădire, în ciuda unui nume cu rezonanță tehnică: Additive Manufacturing Campus. Pe scurt, AM Campus.
Pe larg, Additive Manufacturing este termenul sub care mai este cunoscut procesul de printare 3D la nivel industrial. BMW are deja o experiență de peste 30 de ani în acest domeniu, însă AM Campus a fost inaugurat oficial în 2020 și este un centru care reunește producția de prototipuri de componente și producția de componente de serie prin tehnologia de printare 3D. Astfel, uzina s-a alăturat celor peste 30 de unități de producție pe care Grupul BMW le are în întreaga lume și unde produce modele BMW, Mini și Rolls-Royce, dar și motociclete sub brandul BMW Motorrad. În total, constructorul german are aproape 120.000 de angajați la nivel global.
Noul centru AM Campus are circa 50 de sisteme industriale cu ajutorul cărora BMW printează în format 3D cel puțin 50.000 de componente de serie anual.
Așa cum aveam însă să descopăr în timpul vizitei, procesul de printare 3D este unul complex și începe, în realitate, cu o analiză detaliată a componentelor și părților care pot fi produse fizic prin tehnologia de printare 3D. Și, mai ales, componente care permit obținerea unor beneficii majore comparativ cu producția convențională. Selecția finală este realizată de ingineri, dar se bazează în mare parte pe o serie de date despre componentele respective care sunt analizate cu un algoritm de machine learning pentru a face o preselecție a celor mai bune componente.
Urmează proiectarea efectivă a componenței care va fi realizată prin printare 3D cu ajutorul unor aplicații software dedicate, care împart componenta în “straturi” digitale extrem de subțiri. Ulterior, sistemele industriale sunt programate pentru a parcurge întregul proces de printare 3D, strat cu strat.
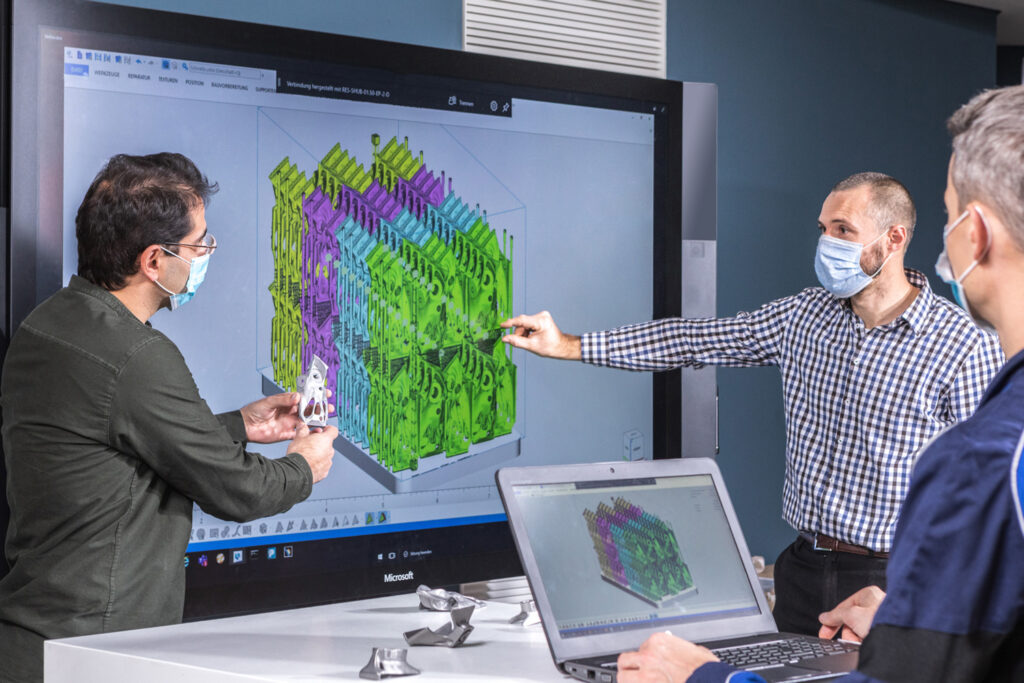
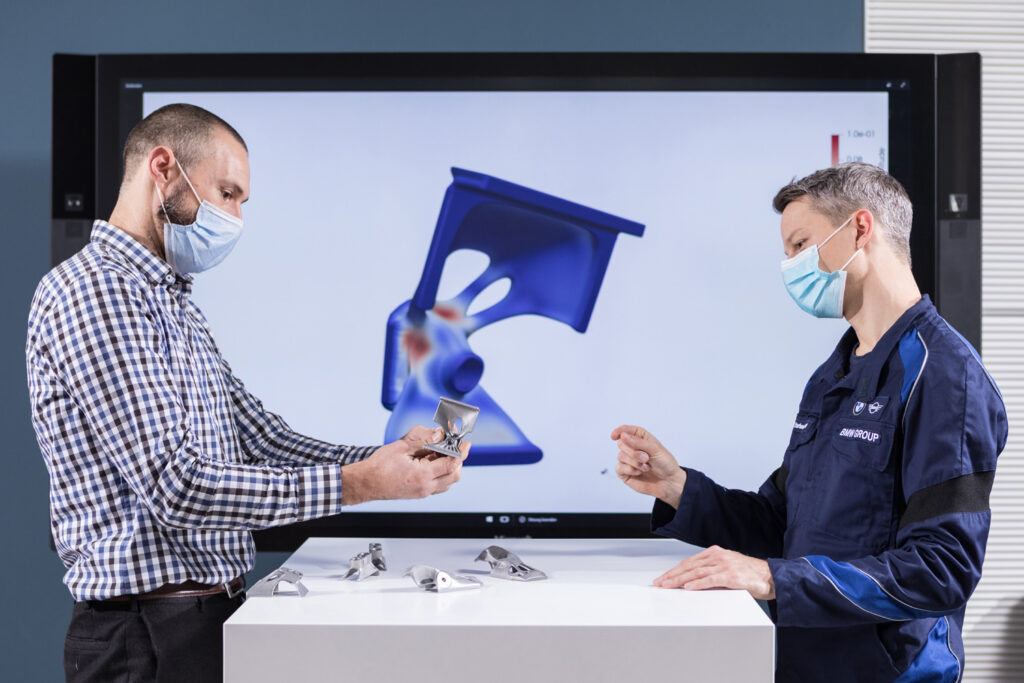
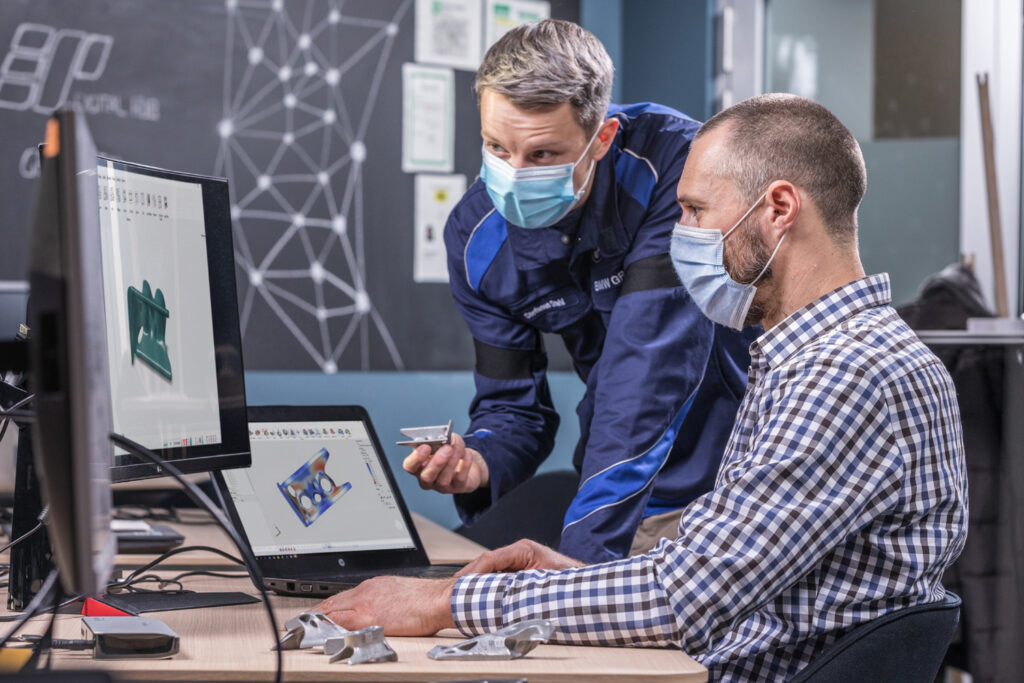
În cadrul vizitei de la AM Campus am putut vedea procesul de printare 3D în plină desfășurare în două hale distincte: una care produc componente 3D din metal – în special din aluminiu și silice, dar și alte materiale – și altă hală care produce componente 3D din plastic. Totuși, procesul în sine este destul de asemănător: producția componentei se realizează printr-o varietate de procese. În funcție de componentă, materia primă inițială sub formă de pudră este plasată pe “podeaua” sistemului și formează practic baza în care un laser trasează contururile geometrice ale componentei respective.
Laserul respectiv topește complet sau parțial materialul sub formă de pudră, iar procesul se repetă pentru fiecare strat în parte, așa cum au fost definite în aplicația software. O componentă poate avea și până la 4000 de astfel de straturi, care sunt construite unul câte unul de mașinăriile special programate în acest sens. La final, după ce straturile se răcesc, acestea se solidifică și dau forma finală a componentei printată 3D. În prezent, un astfel de sistem are 4 lasere, însă în viitor BMW va utiliza sisteme cu câte 10 lasere, ceea ce va avea ca efect o creștere a ratei de producție. Alternativ, procesul poate avea loc și prin intermediul unei imprimante 3D care adăugă material strat cu strat.
De asemenea, pe parcursul lanțului de producție, produsele rezultate sunt transportate prin sisteme automatizate între diversele sisteme de producție, fără intervenție umană. În acest fel, procesul de producție este mult mai eficient și rapid și, din acest motiv, centrul AM Campus are numai 80 de angajați care lucrează într-o singură tură. Acest proces de automatizare a redus deja costurile totale cu circa 50%.
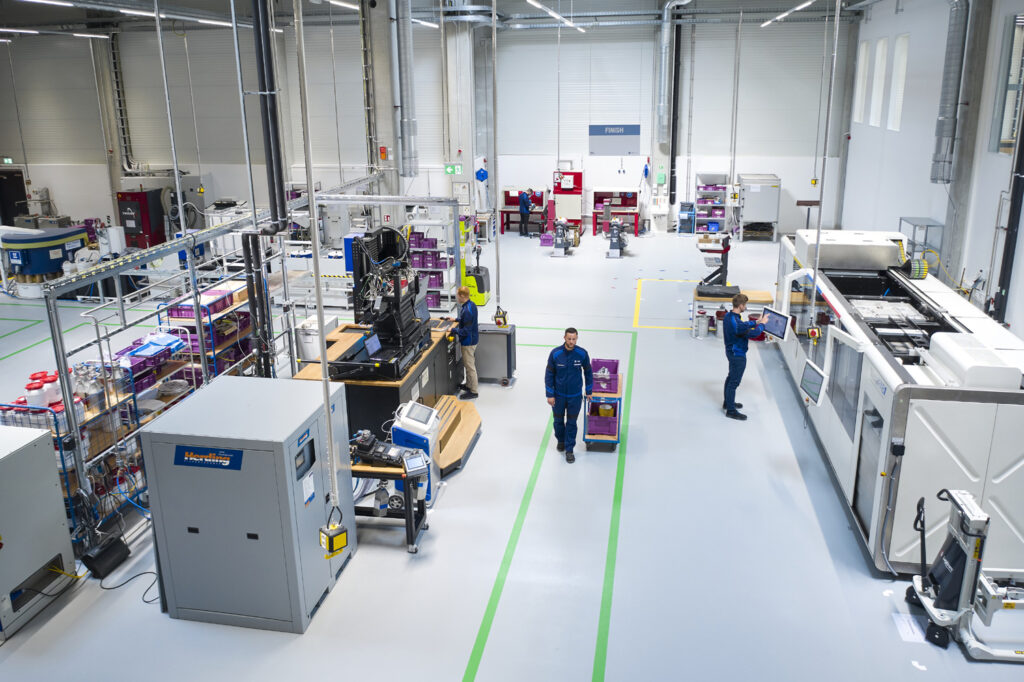
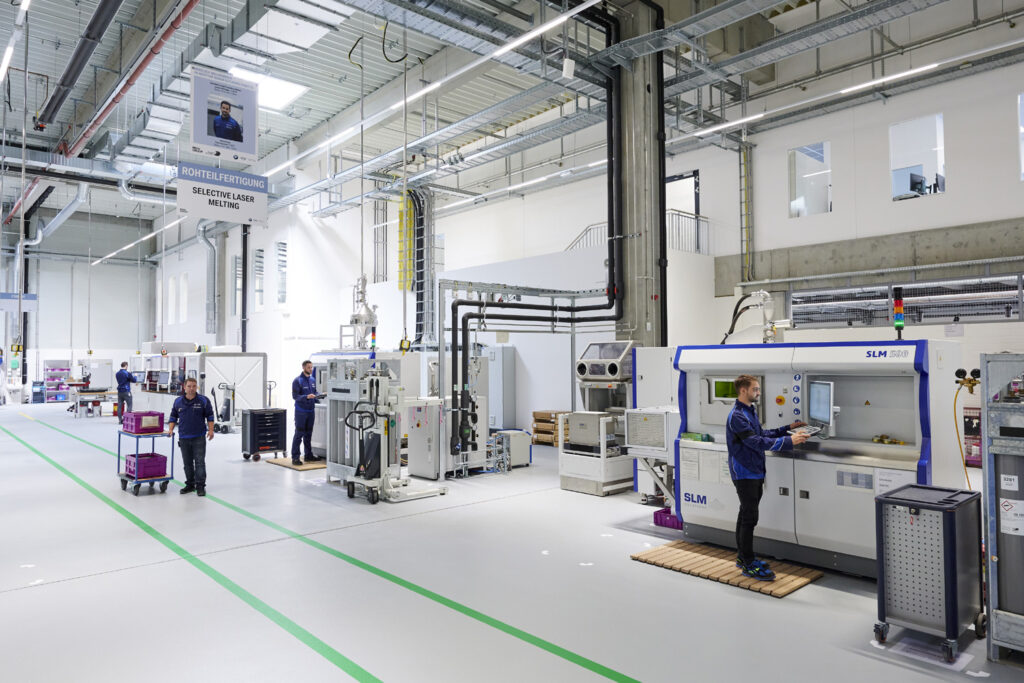
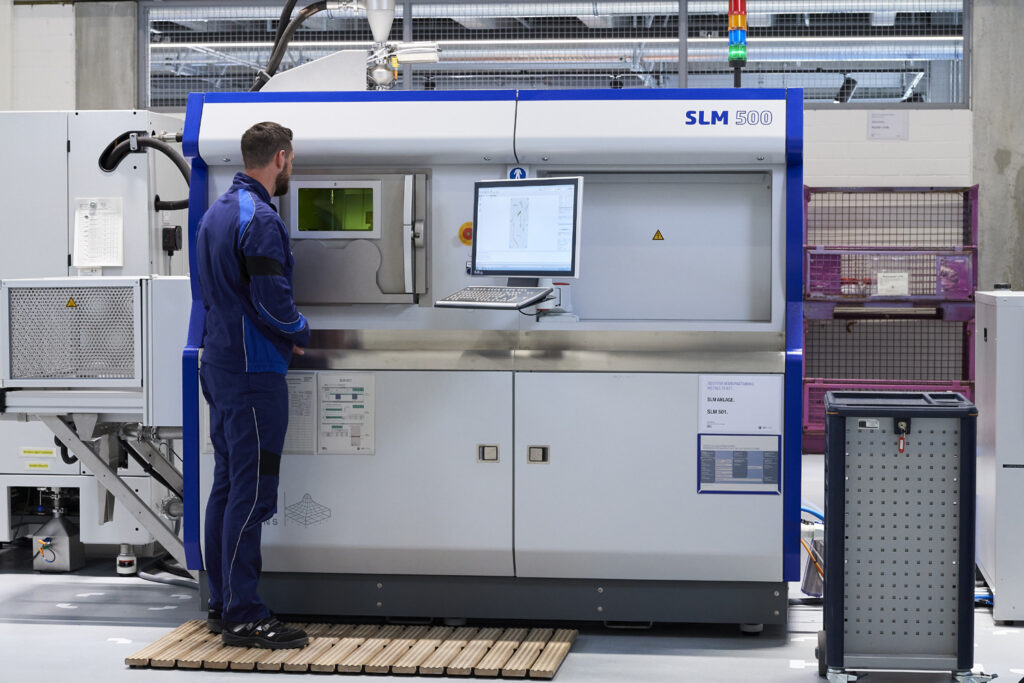
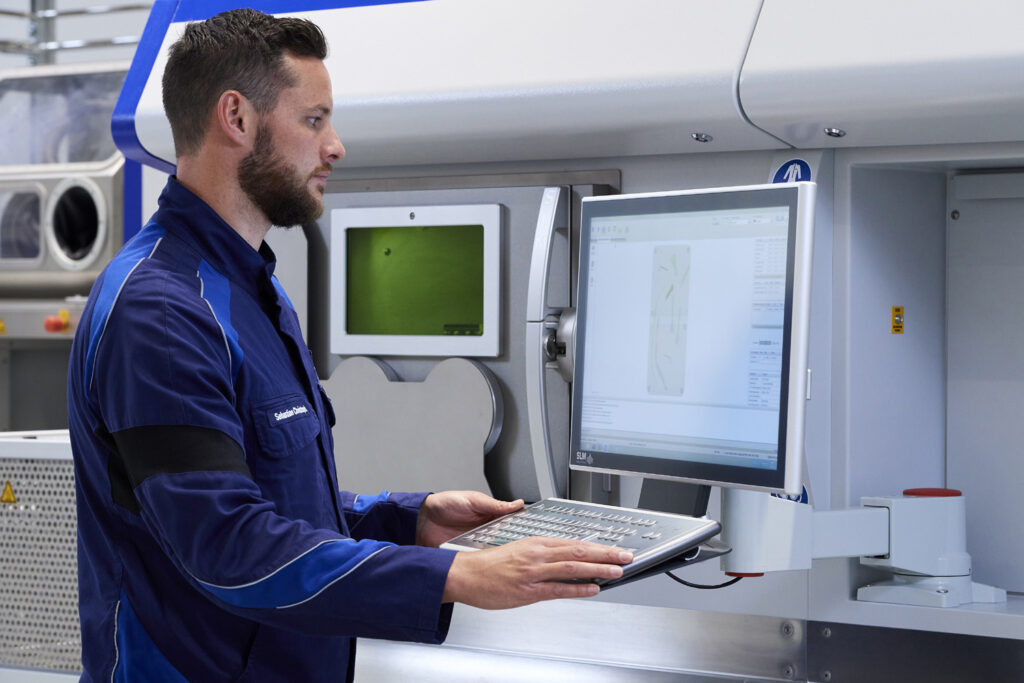
În principal, la AM Campus sunt concepute și produse diverse componente prin printare 3D care sunt folosite pentru diverse modele ale constructorului britanic Rolls-Royce, parte a Grupului BMW, în special pentru șasiul lui Rolls-Royce Ghost. De exemplu, prin această metodă se produc o serie de componente pentru caroserie și pentru celula pasagerului. În plus, tot aici se produc și componente 3D pentru motocicletele care poartă sigla BMW. În alte centre, BMW a produs însă de-al lungul timpului și componente printate 3D pentru modele precum BMW i8 Roadster și MINI John Cooper Works GP, dar și pompa de apă pentru mașinile de curse din Campionatul German de Turisme.
Suntem curioși să aflăm însă mai multe detalii, iar întrebările încep să curgă inevitabil. De exemplu, tehnicienii ne povestesc că “utilizarea tehnologiei de printare 3D la nivel industrial oferă numeroase avantaje: componentele sunt mult mai ușoare comparativ cu cele produse convențional, iar costurile de producție scad cu circa 30% pentru prototipurile de componente și 50% pentru componentele de serie. În plus, pentru anumite componente cu un design complicat, timpul de producție scade de la câteva luni la numai câteva zile. De exemplu, componentele de mici dimensiuni pot fi gata într-un interval de 4 zile, în timp ce componentele de dimensiuni mai mari pot necesita un timp de producție de până la 10 zile.”
Aici, principalul beneficiu apare în cazul prototipurilor de componente. Inginerii testează o gamă variată de geometrii pentru o anumită componentă înainte de a decide designul versiunii de serie, astfel că utilizarea tehnologiei de printare 3D permite reducerea dramatică a timpului total de dezvoltare pentru un nou model.
În hala pentru componente non-metalice, inginerii Grupului BMW ne arată inclusiv ceea ce va deveni, la finalizarea procesului de producție, o cheie de mașină printată 3D. Iau un astfel de prototip în mână, sunt surprins de cât de ușor și fragil este, dar cu toate astea apăs pe el, ca și cum aș apăsa pe butonul de închidere al mașinii. Este momentul în care se aude un zgomot și îmi dau seama că tocmai am reușit performanța de a “sparge” o cheie. Inginerii de lângă mine încep să râdă și mă asigură că paguba produsă este nesemnificativă. Norocul meu.
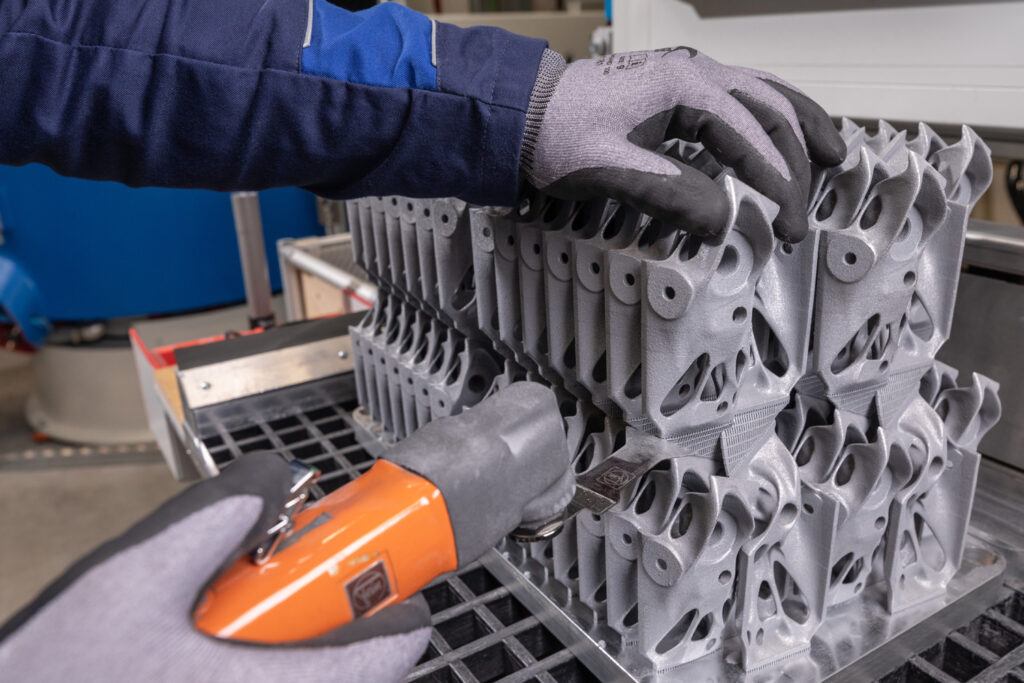
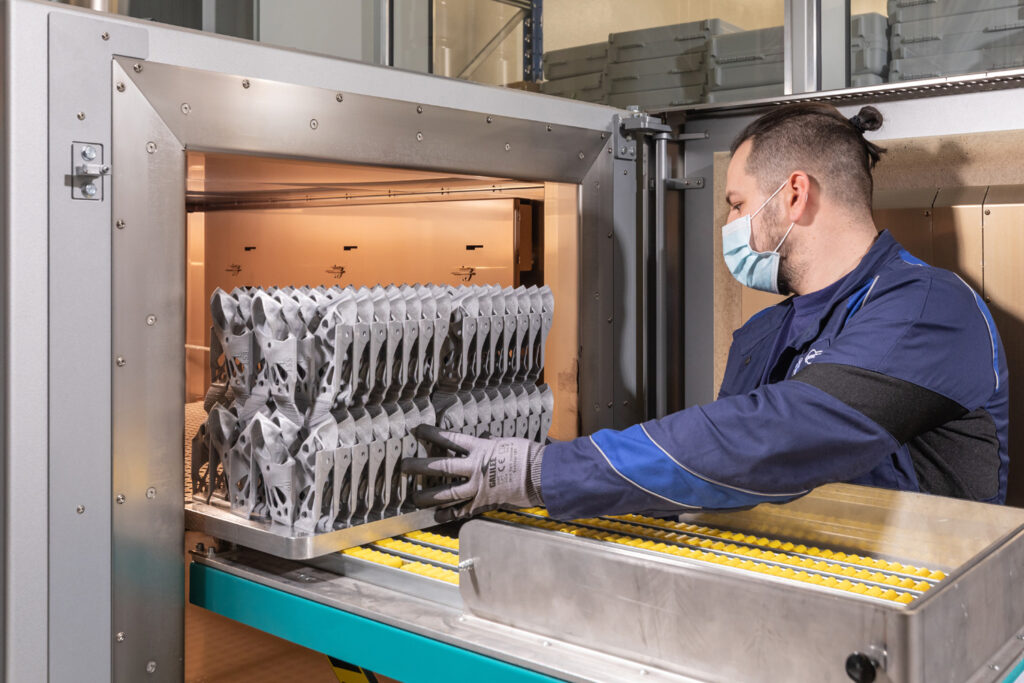
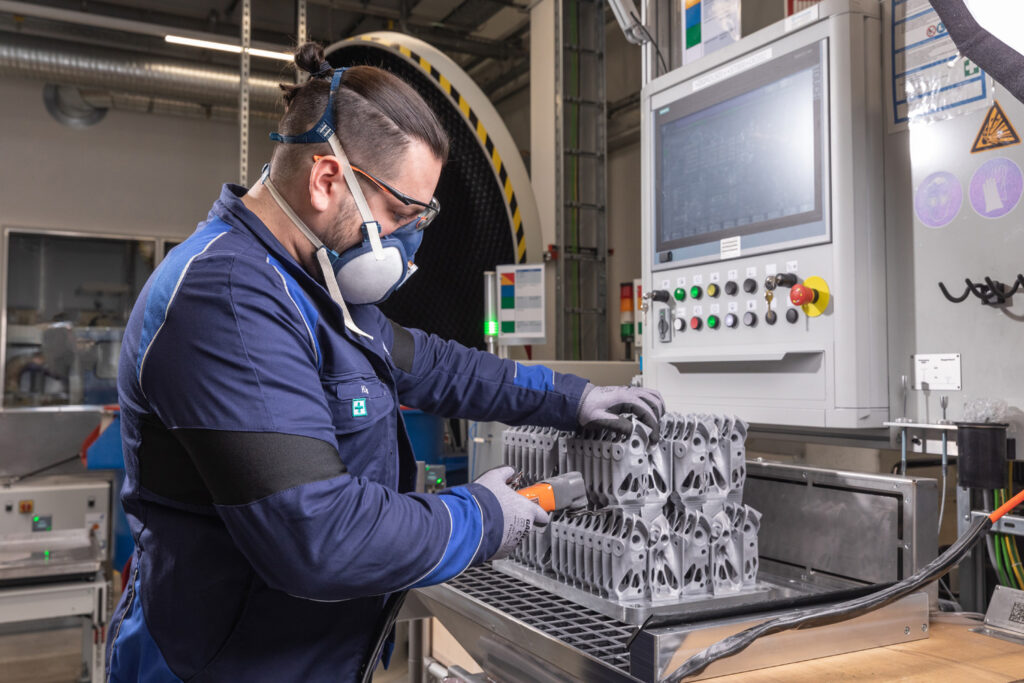
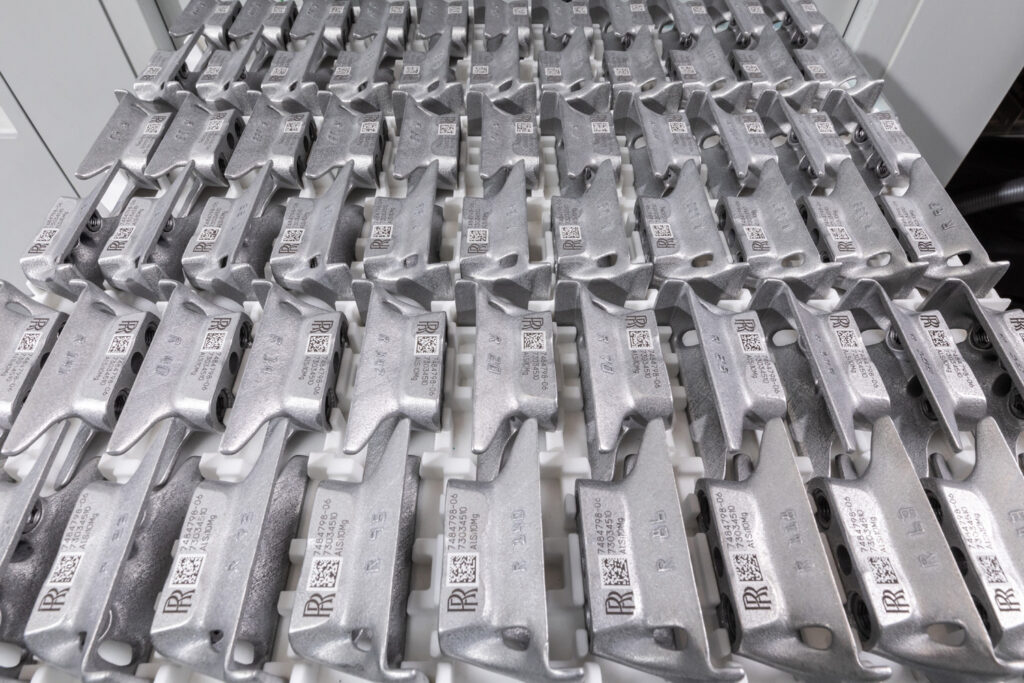
Ne apropiem de finalul workshop-ului practic și, cumva inevitabil, apare și întrebarea dacă, într-un viitor mai mult sau mai puțin îndepărtat, va exista și o mașină produsă integral la o imprimantă 3D industrială. Răspunsul este tranșant. “Nu va exista așa ceva. De exemplu, sticla nu se poate produce cu imprimante 3D. La fel anvelopele, chiar dacă anumite componente ale pneurilor sunt realizate prin printare 3D. Numărul componentelor realizate prin printare 3D crește, dar se înlocuiesc doar componentele pentru care există o justificare tehnică și financiară”.
În mod surprinzător, aflăm că inginerii de la AM Campus învață meseria mai degrabă în mod practic, la fața locului. “Nu prea ai unde să înveți o astfel de tehnologie în universități, pentru că tehnologia pe care o folosim este foarte nouă. Angajații învață din mers, mai ales că proiectele se schimbă mereu. Nu căutăm oameni cu anumite abilități, iar în prezent avem aici inclusiv mecanici clasici care au învățat cum funcționează mașinăriile și au făcut reconversie profesională”.
Una dintre provocările generate de o tehnologie nouă este că apar frecvent probleme în procesul de producție, motiv pentru care controlul calității este foarte important. Controlul calității este parțial automatizat, însă verdictul final este oferit de un angajat în carne și oase. Cel puțin pentru moment.
Și dacă ești tentat să crezi că o componentă 3D nu are ce caută într-o mașină, mai ales într-una premium sau de lux, inginerii BMW ne liniștesc pe deplin și ne spun că tehnologia este deja utilizată cu succes și în domenii mult mai sensibile precum sisteme de apărare militară, sisteme medicale sau în industria aeronautică.
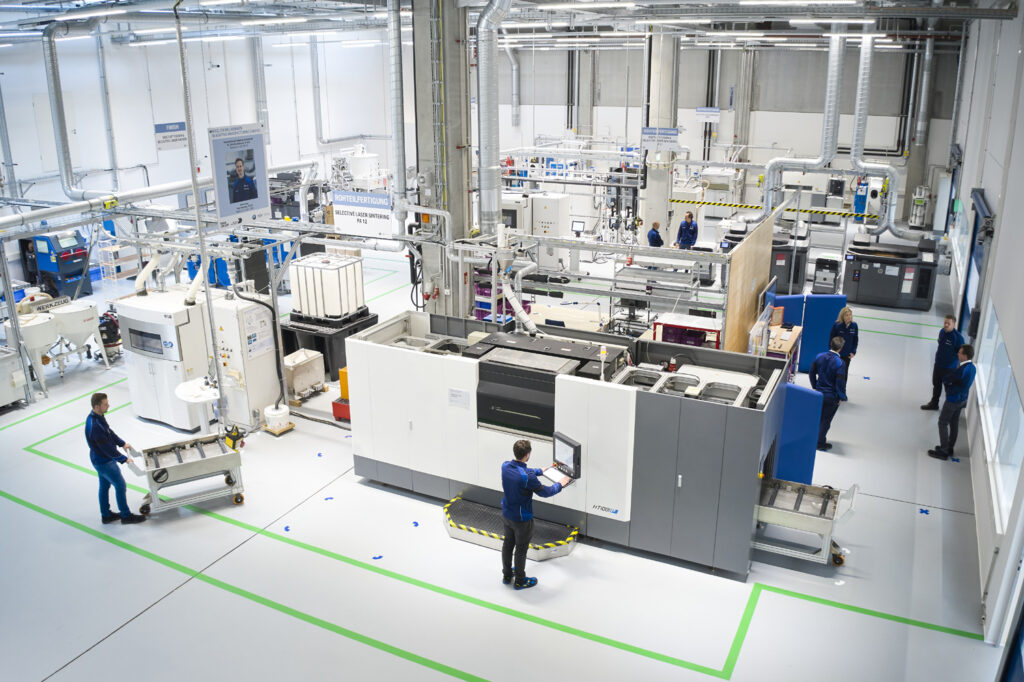
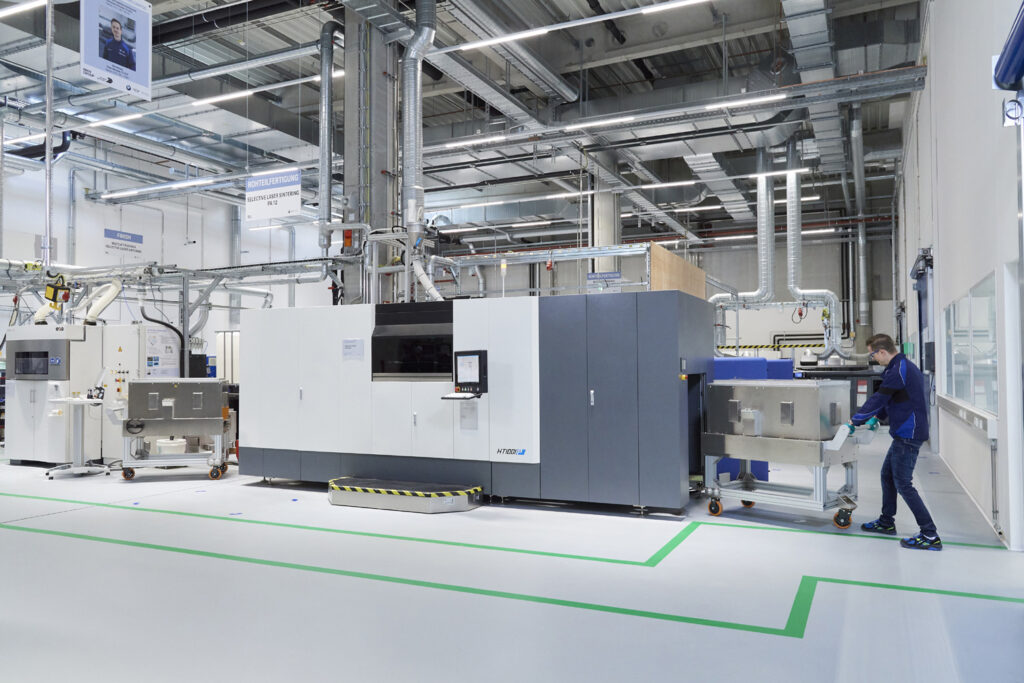
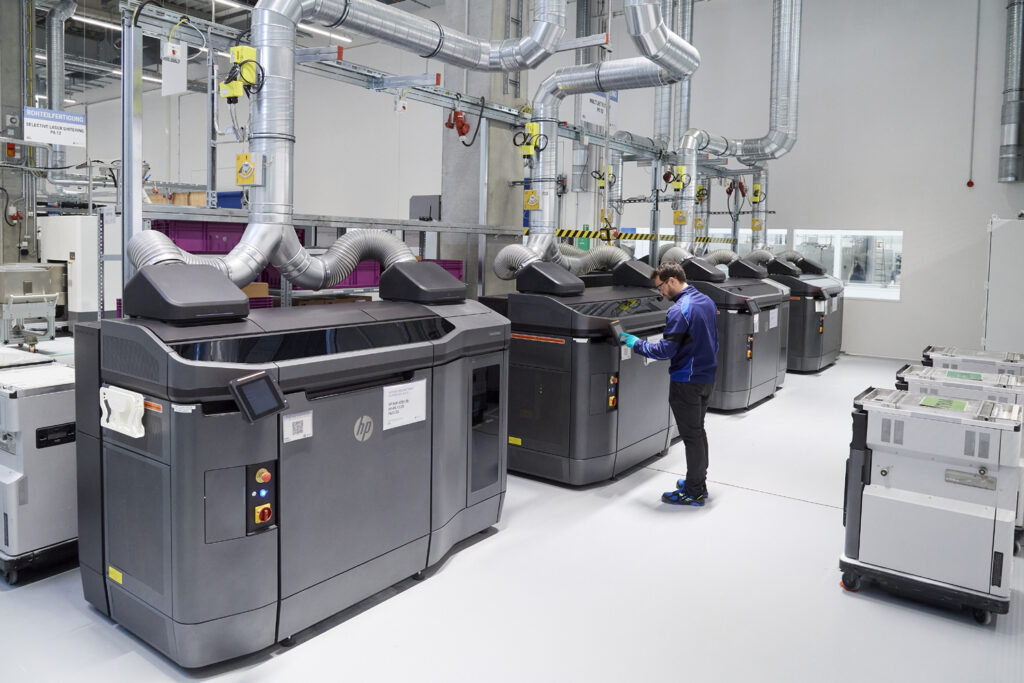
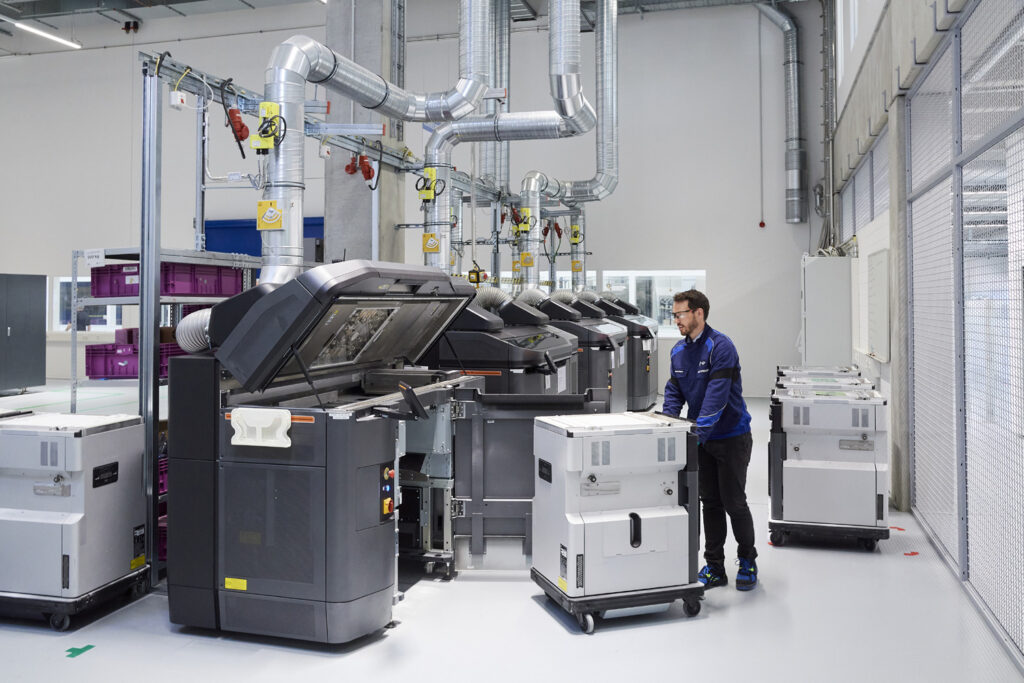
Uzina din Dingolfing
Una dintre glumele pe care le fac ocazional cu unul dintre colegii din redacția Autocritica este că Dingolfing este un oraș din China. Nu e vina noastră, pur și simplu cuvântul are mai degrabă o rezonanță asiatică decât europeană.
În realitate, Dingolfing este un orășel german situat la circa 100 de kilometri nord-est de Munchen unde locuiesc aproximativ 20.000 de locuitori. Tot aici se află însă și o uzină a Grupului BMW. Și nu orice uzină, ci chiar cea mai mare uzină a Grupului BMW din Europa, dezvoltată pe o suprafață de circa 280 de hectare.
În total, aici lucrează circa 17.000 de angajați, adică aproape la fel de mulți ca numărul de locuitori ai orășelului. Pentru a nu bulversa traficul din micuța localitate, BMW transportă zilnic angajații cu circa 270 de autobuze.
De altfel, în drumul nostru spre uzină, suntem martori la o astfel de descindere a forței de muncă. Ne strecurăm cum putem și suntem preluați de Alexander Bachner, gazda noastră pentru vizita la uzină.

Tehnici moderne de vopsire
La Dingolfing se produc modele precum Seria 4, Seria 5, Seria 6, Seria 7 – inclusiv versiunea electrica i7 – Seria 8 și iX, iar prima noastră vizită este la vopsitorie, unde procesul este practic complet automatizat.
Procedura clasică de vopsire este cea de atomizare, un proces prin care un braț robotic se “servește” singur cu o cantitate de vopsea calculată individual pentru fiecare mașină în parte și pe care o transformă în picături foarte fine atunci când o împrăștie pe suprafața caroseriei printr-o serie de mișcări prestabilite.
Un astfel de braț robotic face undeva între 35.000 și 55.000 de rotații pe minut, iar picăturile foarte fine de vopsea aderă electrostatic pe caroserie. De altfel, “electrostatic” este cuvântul cheie aici, întrucât acest fenomen fizic permite celor de la BMW să vopsească caroserii de diverse culori una după alta, chiar dacă acestea sunt foarte apropiate pe linia de producție. “Nu există nicio șansă ca picăturile de vopsea albastră să ajungă pe caroseria de lângă, vopsită într-o nuanță de gri”, ne explică zâmbind Bachner.
De la sfârșitul anului trecut, Grupul BMW a trecut însă la nivelul următor în ceea ce privește procesul de vopsire, unul care nu se folosește de fenomenul electrostatic. În schimb, noul proces de vopsire se bazează pe aplicarea unor jeturi de vopsea cu grosimi cuprinse între un milimetru și 50 de milimetri printr-o serie de orificii.
Pentru un constructor precum BMW, principalul avantaj este că acest proces de vopsire permite utilizarea a două culori diferite de vopsea pentru aceeași mașină fără să mai fie nevoie ca anumite părți ale caroseriei să fie mascate manual pentru a evita împrăștierea vopselei. În plus, BMW poate folosi această tehnologie pentru un grad mai mare de personalizare a culorilor pentru caroserie din partea clienților. Pentru moment, acest proces nou este folosit la scară mai mică, doar pentru modele precum BMW M4 Coupe, însă procesul urmează să fie extins treptat și pentru alte modele produse la Dingolfing.
Automatizarea completă a acestui proces are și alte efecte benefice: la fiecare 7000 de ore de utilizare, consumul de energie electrică este cu 6.000 MWh mai mic, iar emisiile de dioxid de carbon scad cu aproape 2.000 de tone pe an.
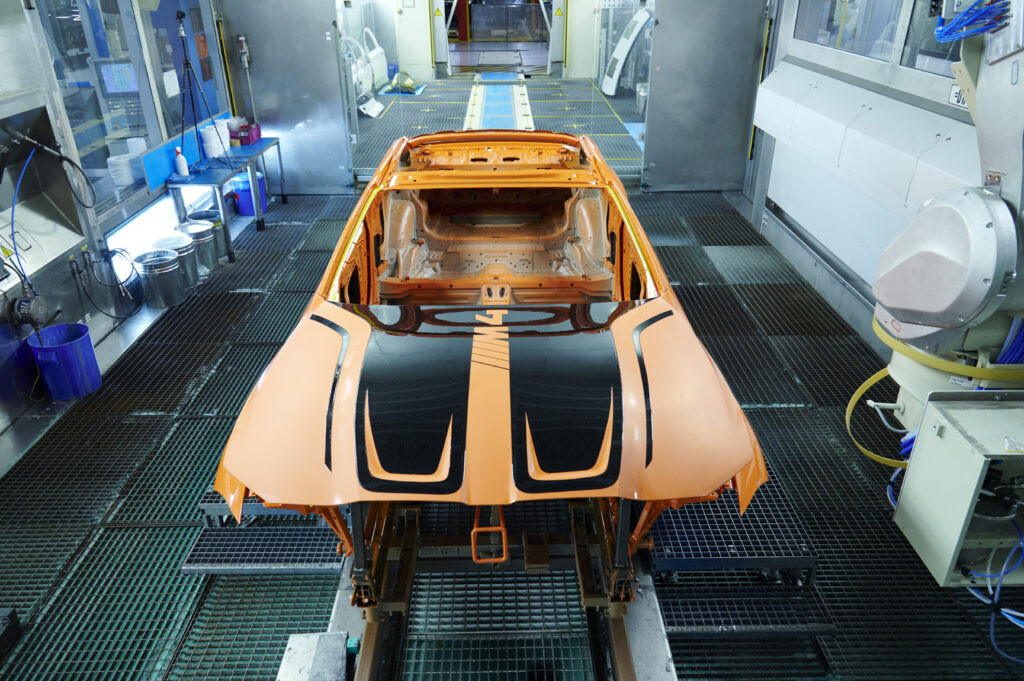
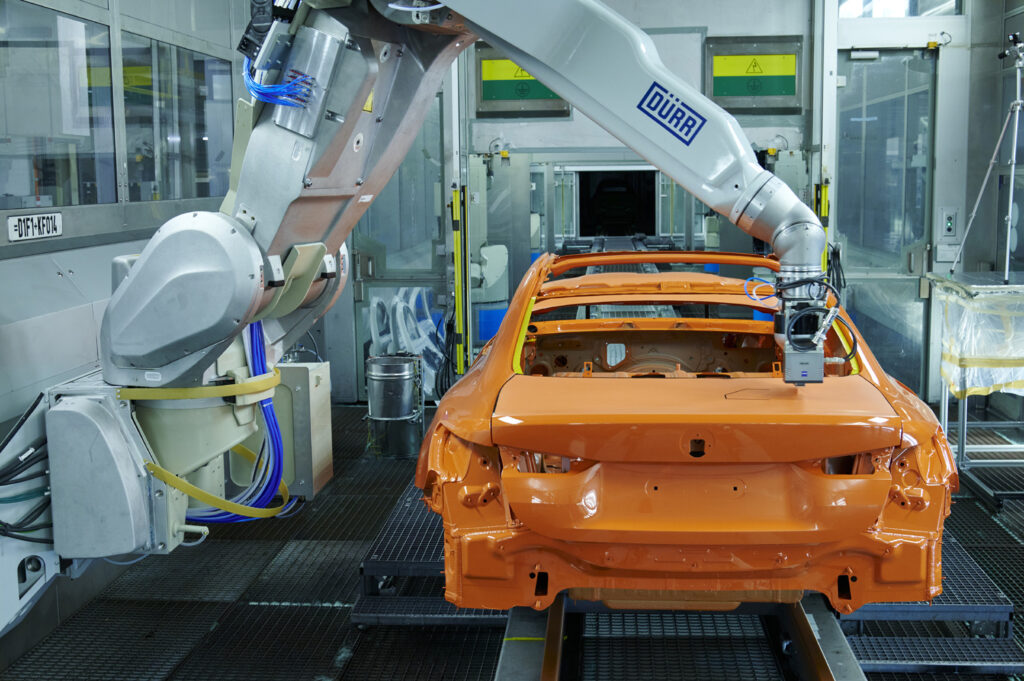
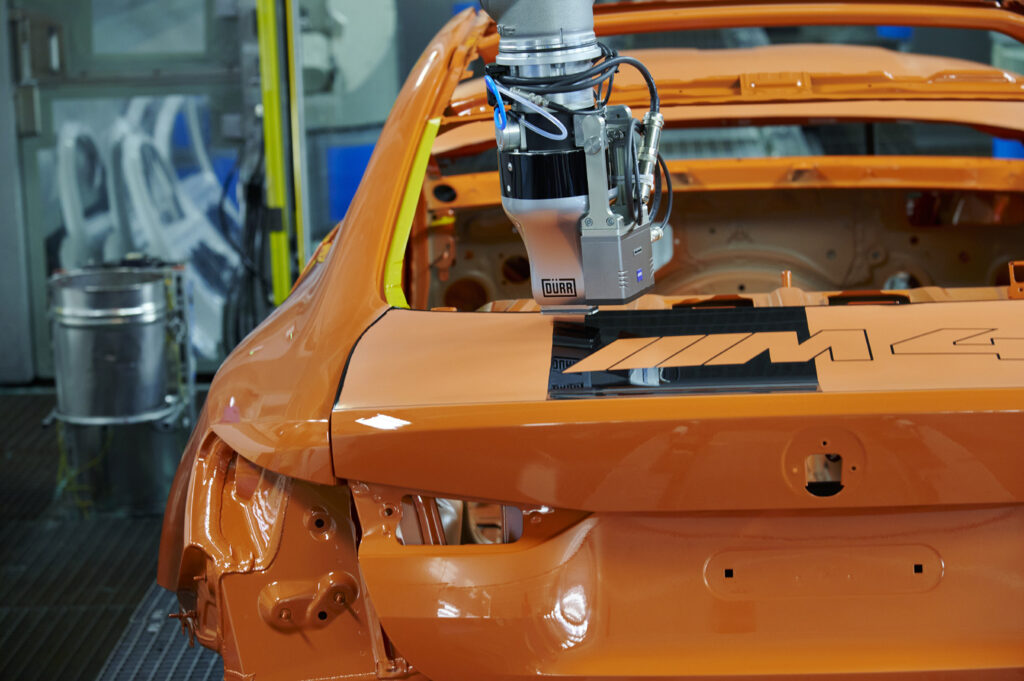
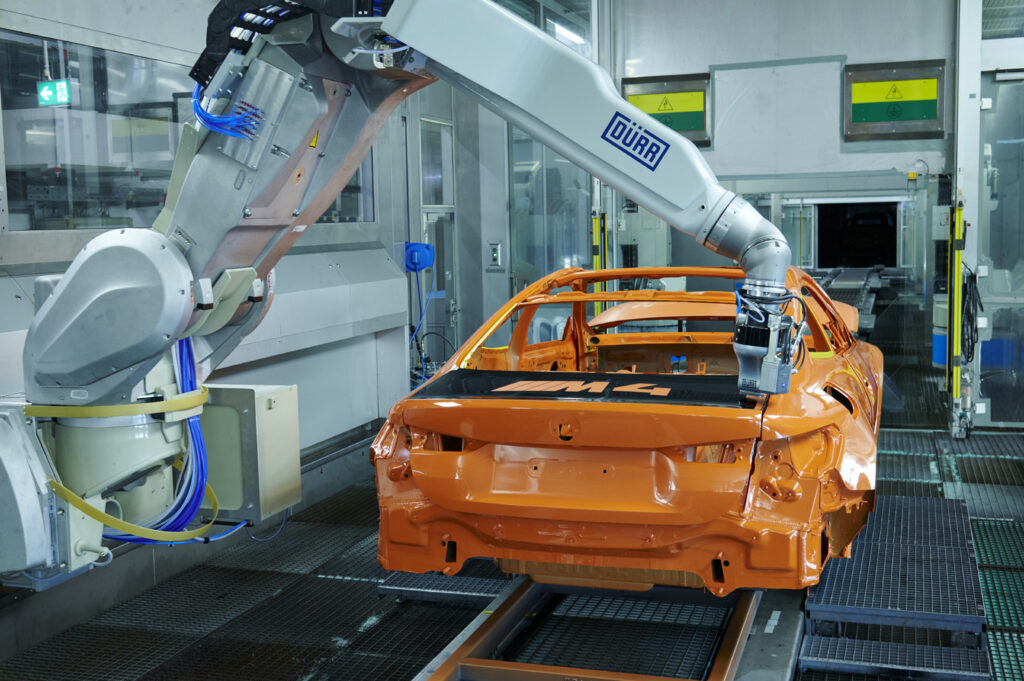
Procesul de asamblare
De la vopsitorie trecem relativ repede printr-o zonă în care surprindem roboții care asamblează portiere pentru numeroase modele. Și aici munca este automatizată în cea mai mare parte, cu o intervenție minimă din partea personalului uman și cu numeroși roboți care parcurg coridoarele pentru a transporta diverse componente. Bachner ne povestește că acești roboți au început să fie folosiți în urmă cu 5 ani, când aveau o viteză extrem de mică din motive de siguranță, pentru a evita producerea unor accidente.
Ieșim, intrăm și ajungem astfel într-una dintre cele mai spectaculoase zone ale uzinei germane: locul în care se asamblează efectiv noile mașini care vor ajunge la clienți. Suntem chiar în zona în care se finalizează echiparea șasiului cu radiatorul, instalat manual de angajați, pentru ca apoi șasiul să meargă mai departe pe linia de producție până în zona în care, de pe o linie de producție aflată la un nivel superior, se coboară încet caroseria deja vopsită. Și aici există mai multe zone distincte în care angajații fac ultimele reglaje și se asigură, cu ajutorul unor sisteme electronice, că totul este pus la punct.
Unul dintre lucrurile pe care le observ inevitabil în acest peisaj este diferența majoră dintre viitoarele unități cu motoare electrice și cele cu motoare termice. Pentru că motoarele electrice au dimensiuni mult mai mici decât cele termice și nu necesită instalarea radiatoarelor, ceea ce înseamnă că procesul de asamblare este de asemenea simplificat.
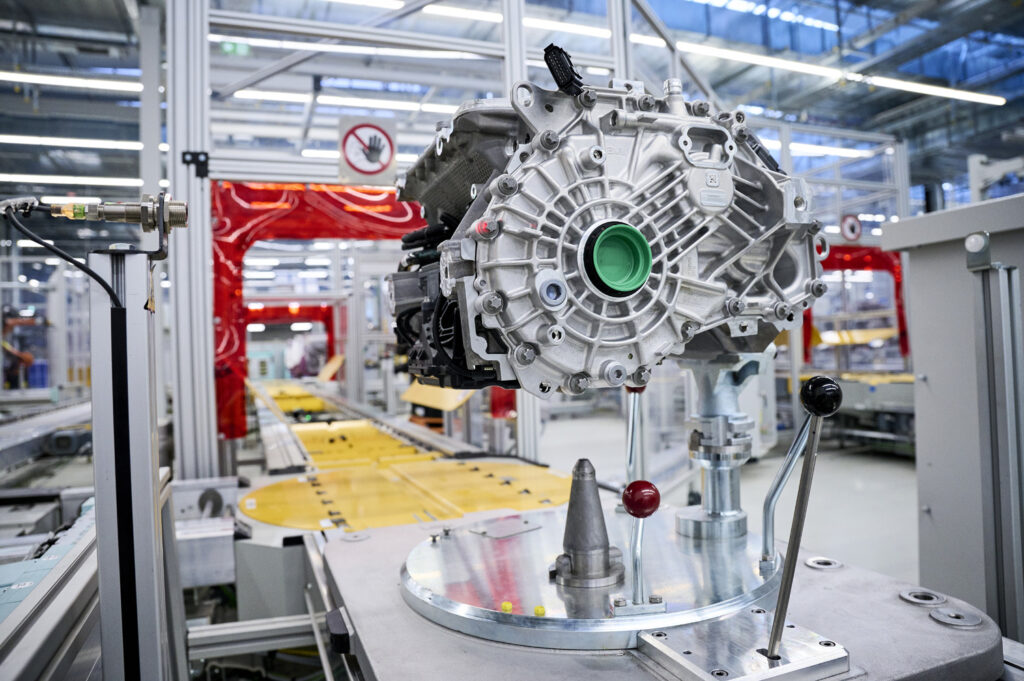
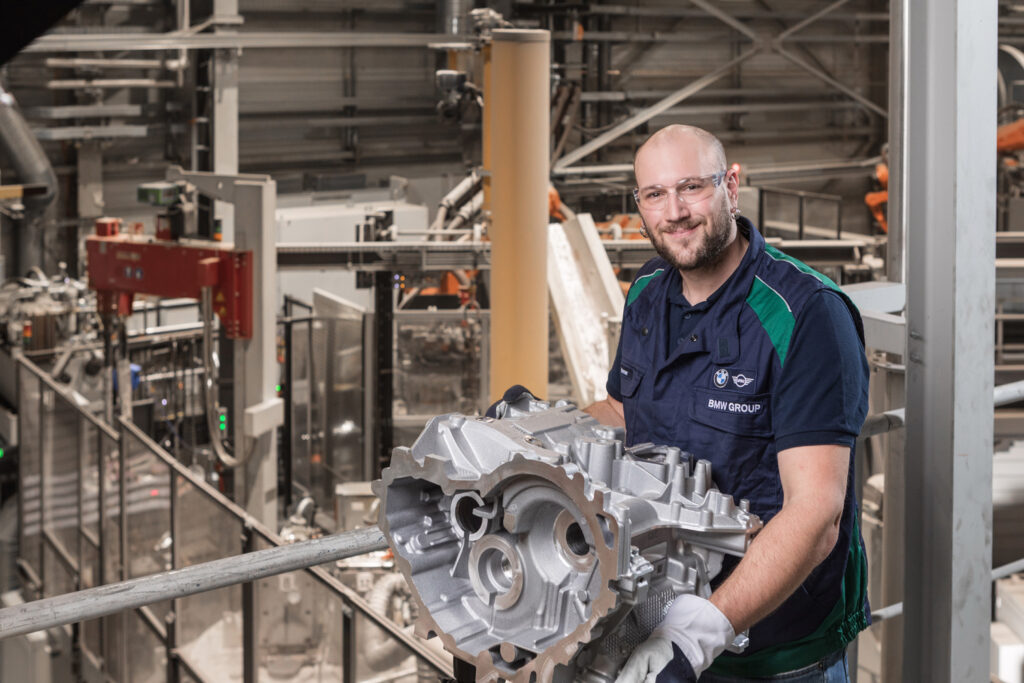
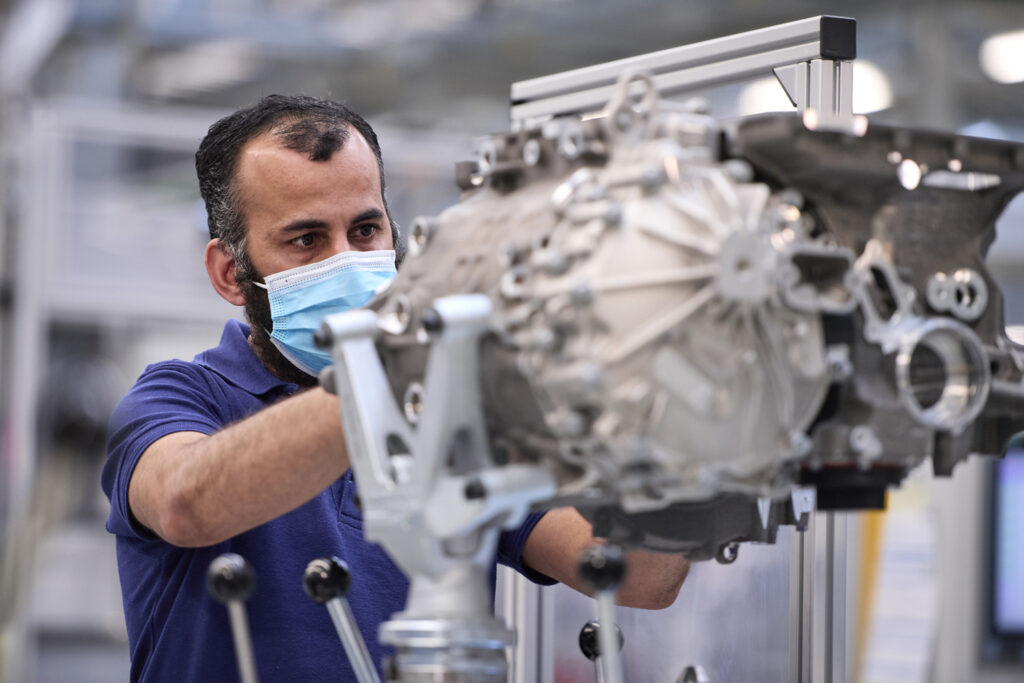
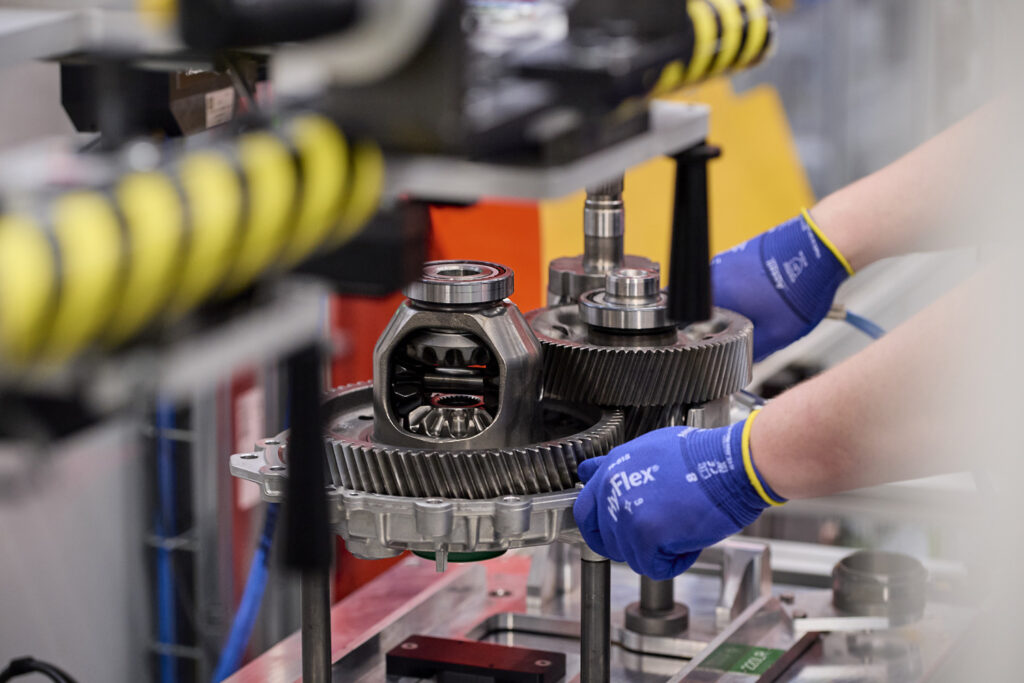
Pe liniile de producție sosesc permanent noi vehicule de toate felurile, în ceea ce aș putea numi haos organizata. Mașinile cu motoare termice sunt intercalate între cele electrice, iar cele mai recente noutăți de pe linia de producție sunt BMW Seria 7, împreună cu versiunea electrică i7, precum și SUV-ul electric BMW iX. Ambele se produc la Dingolfing începând din luna iulie 2022, în aceeași uzină ca și Seria 5 și Seria 8, în ciuda faptului că podeaua liniei de asamblare are o geometrie diferită. Acest lucru permite folosirea la maxim a capacității de producție printr-o adaptare rapidă la comenzile efective primite din partea clienților.
Bachner, omul nostru de legătură în timpul vizitei prin uzină, ne explică faptul că, până la finalul acestui an, 25% dintre vehiculele produse aici vor fi electrice sau plug-in hybrid, iar procentul va crește la 50% până în anul 2025.
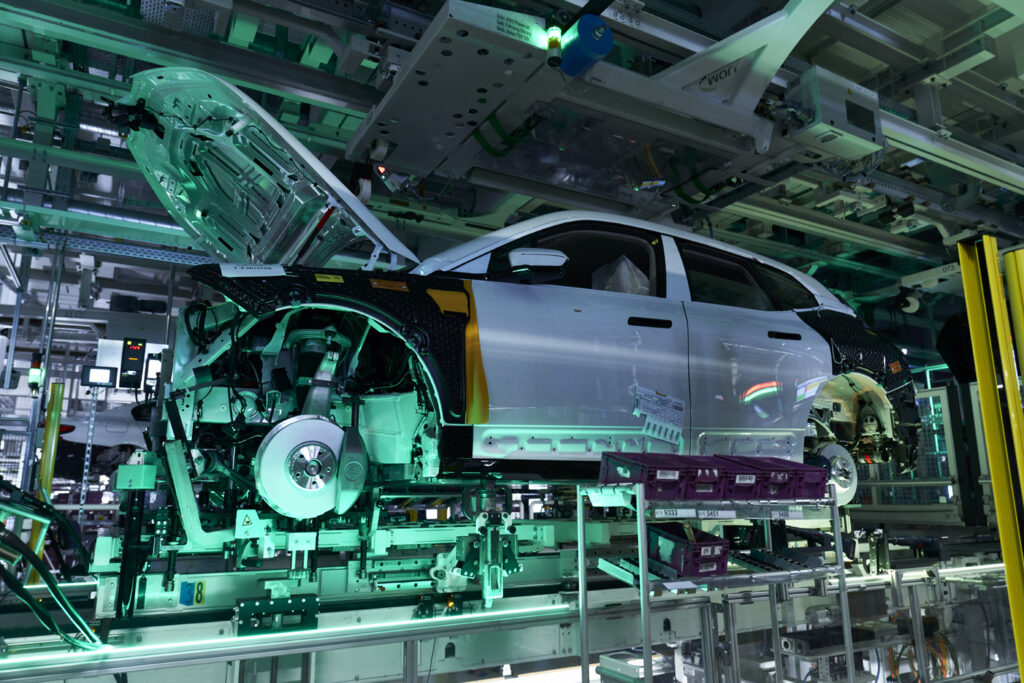
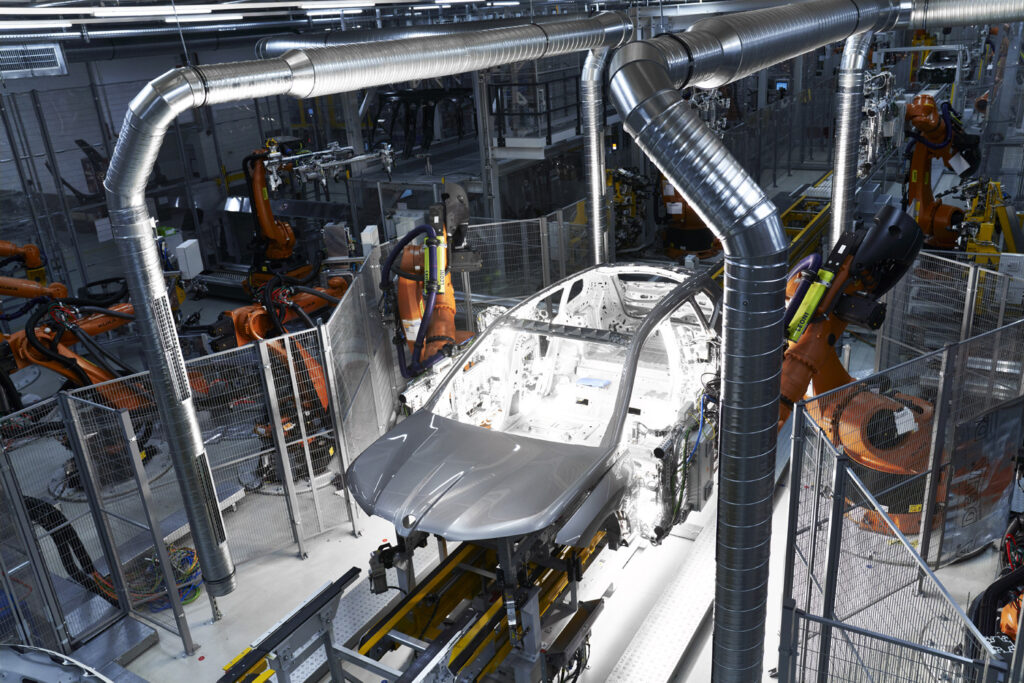
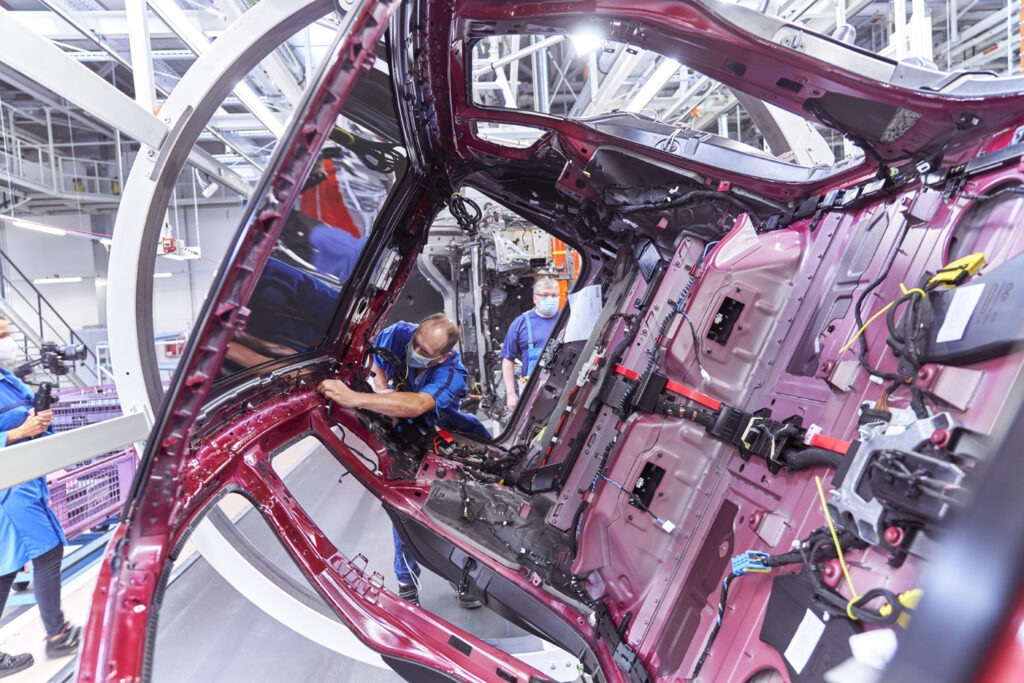
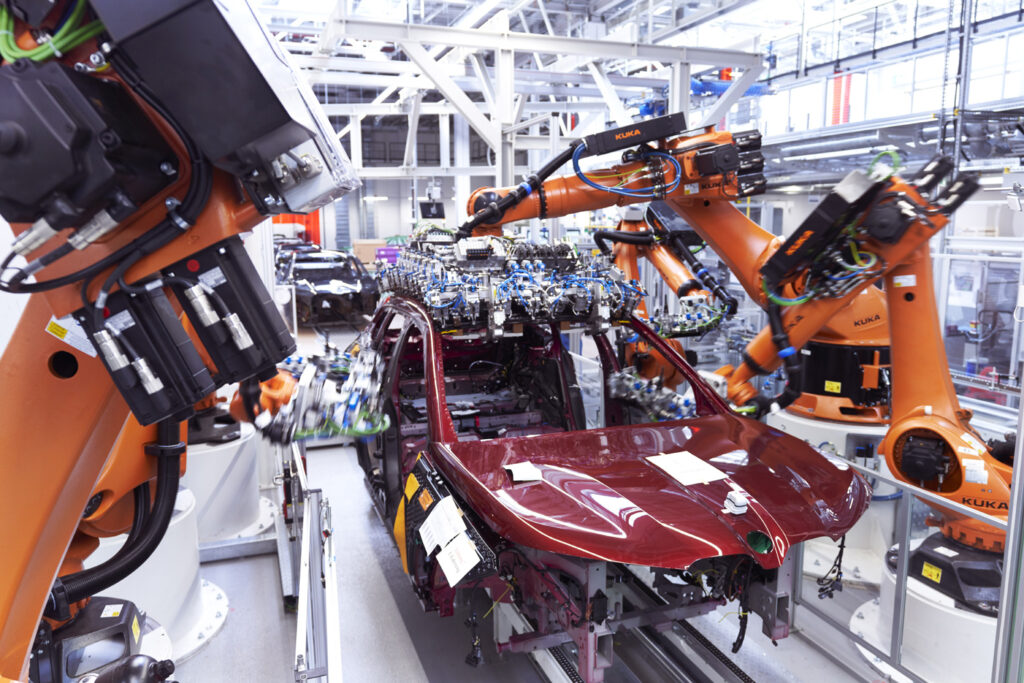

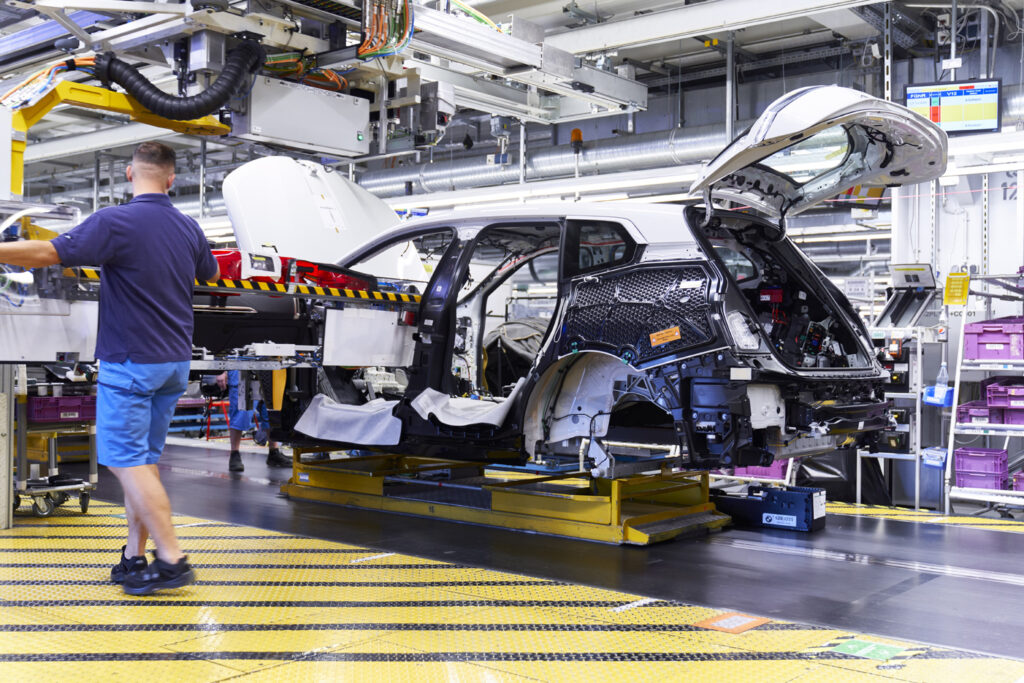
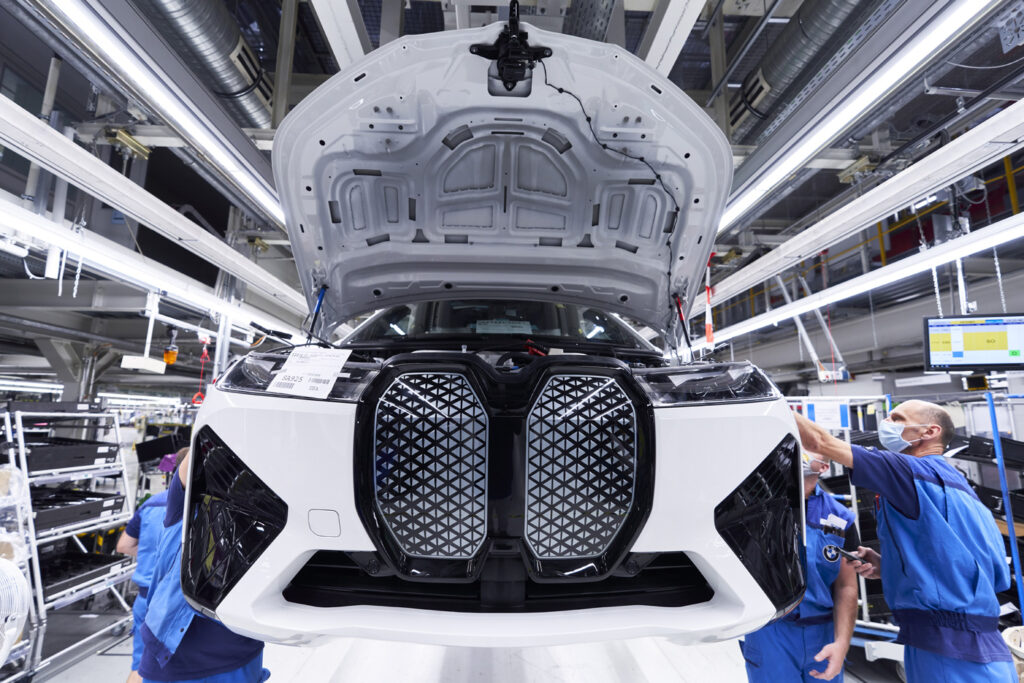
În cazul lui BMW Seria 7, procesul de producție se finalizează cu o inovație: de pe linia de asamblare, vehiculele parcurg în mod autonom o distanță de 170 de metri de la prima pornire a motorului și prima zonă de testare până la zona de ieșire din uzină. Interesant este că acest sistem de pilotaj autonom nu se bazează însă pe sistemele autonome cu care este echipat Seria 7, ci pe o infrastructură externă de camere video și senzori care planifică traiectoria vehiculului.
Din păcate, nu am văzut pe viu acest proces în cadrul vizitei noastre la uzină, care urmează să fie extins treptat și pentru alte modele produse la Dingolfing. Totuși, la finalul vizitei am putut observa testele finale de accelerație și frânare realizate cu șoferi umani pe bancul de probe.
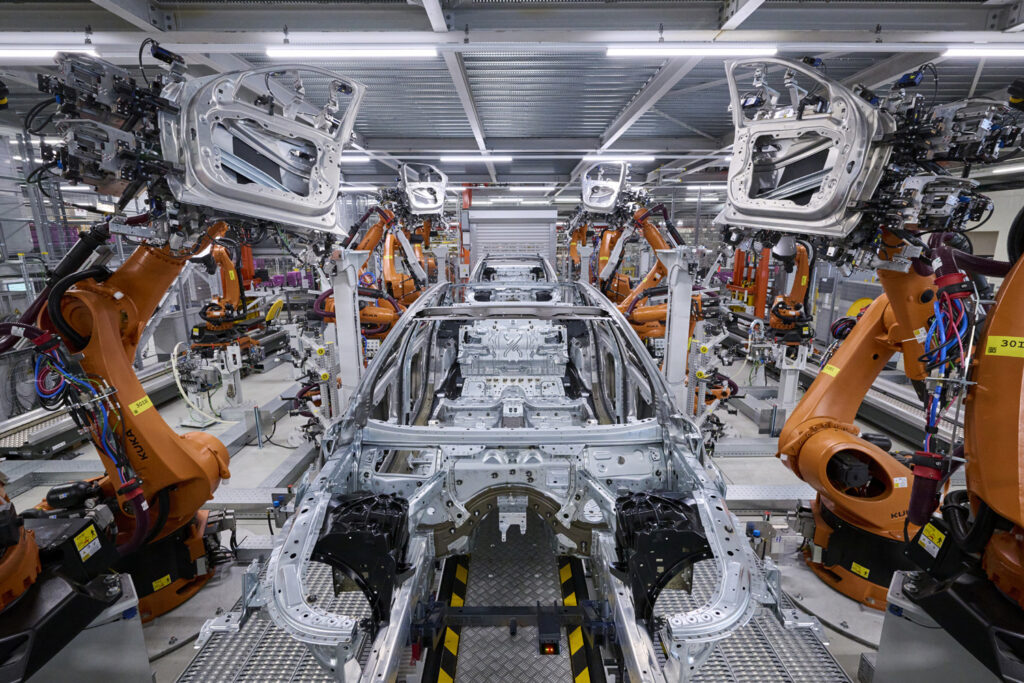

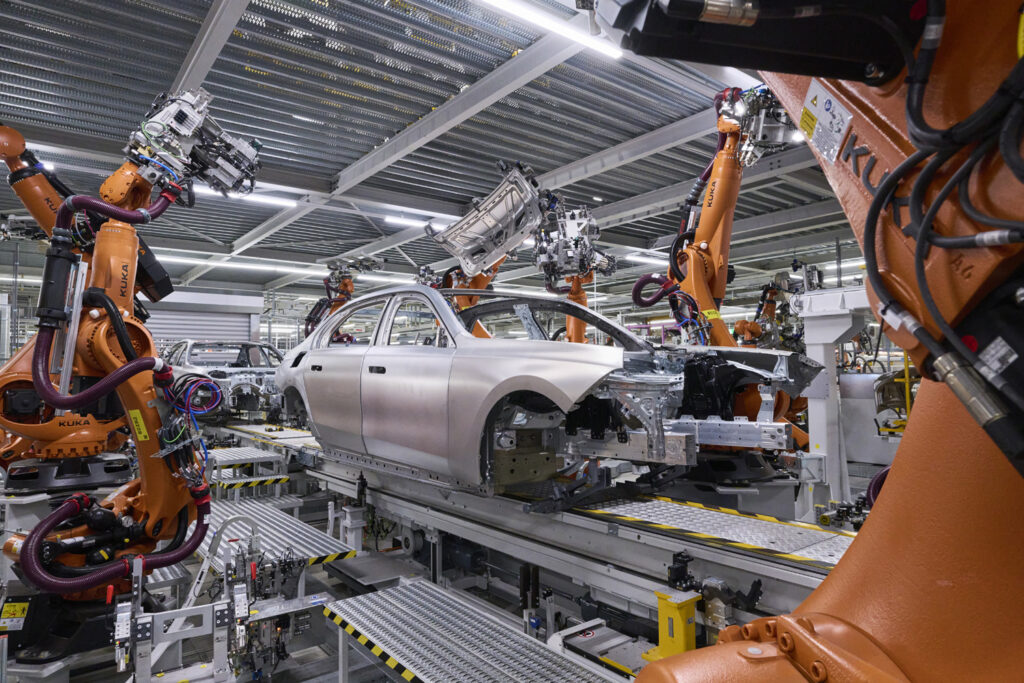
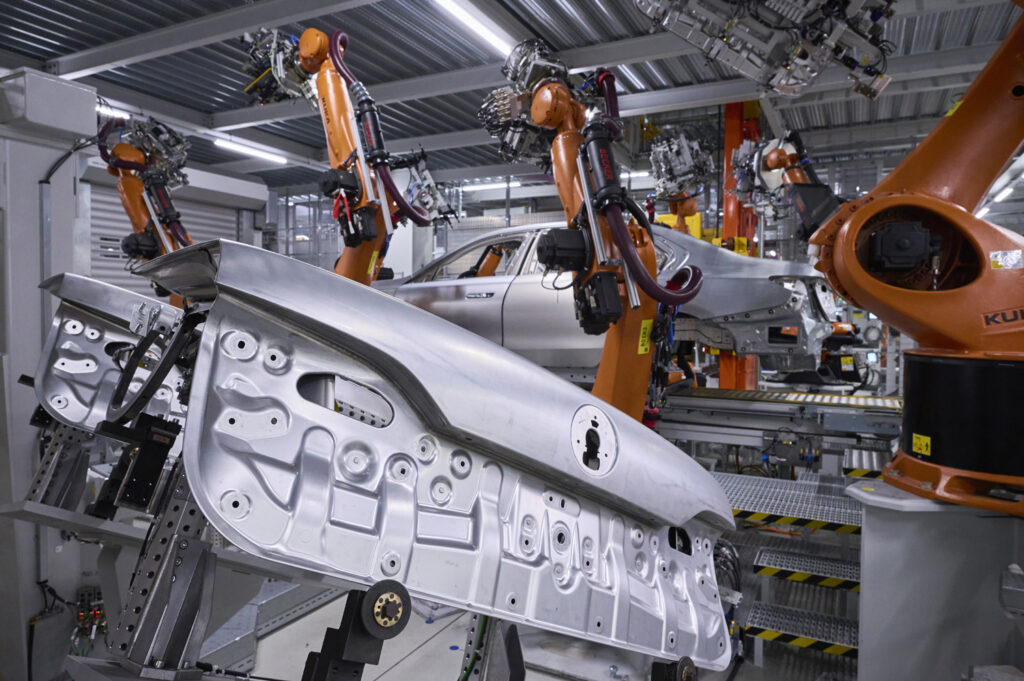
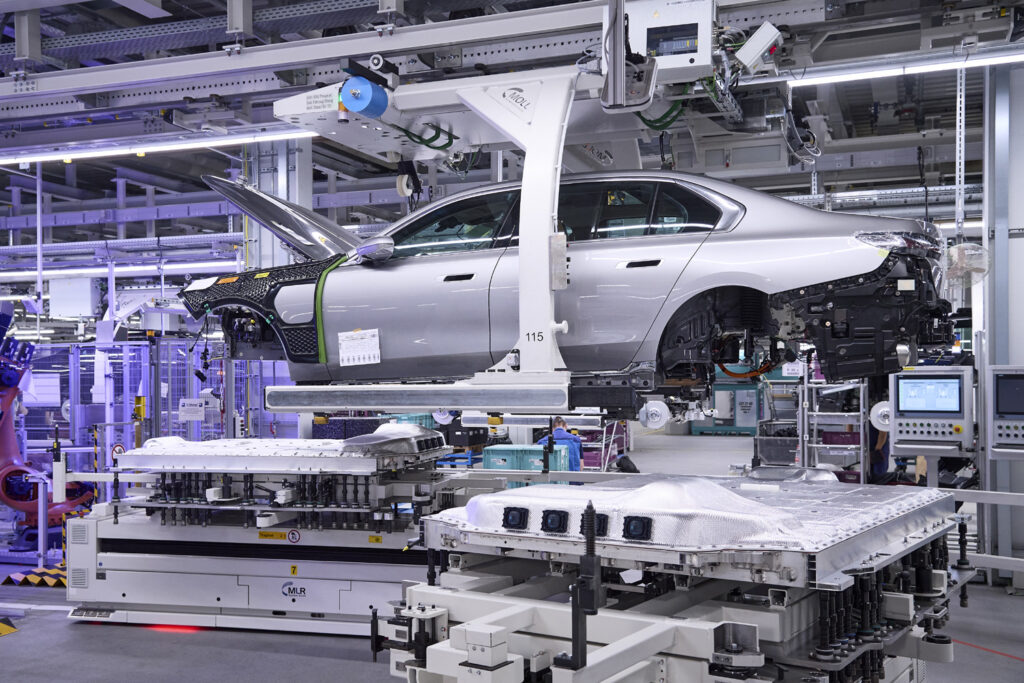
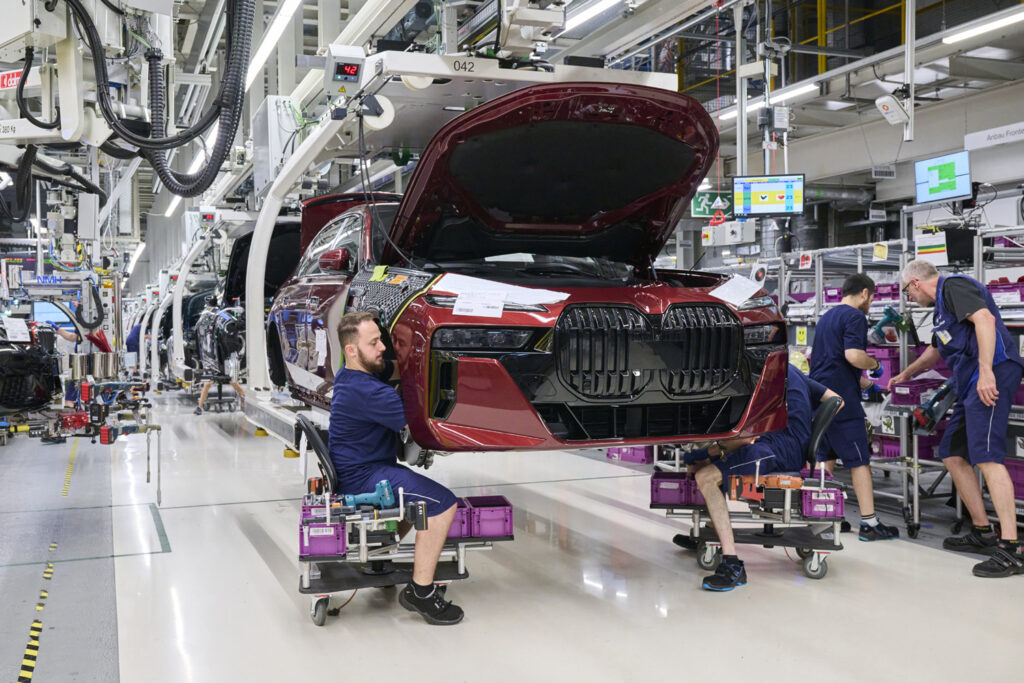
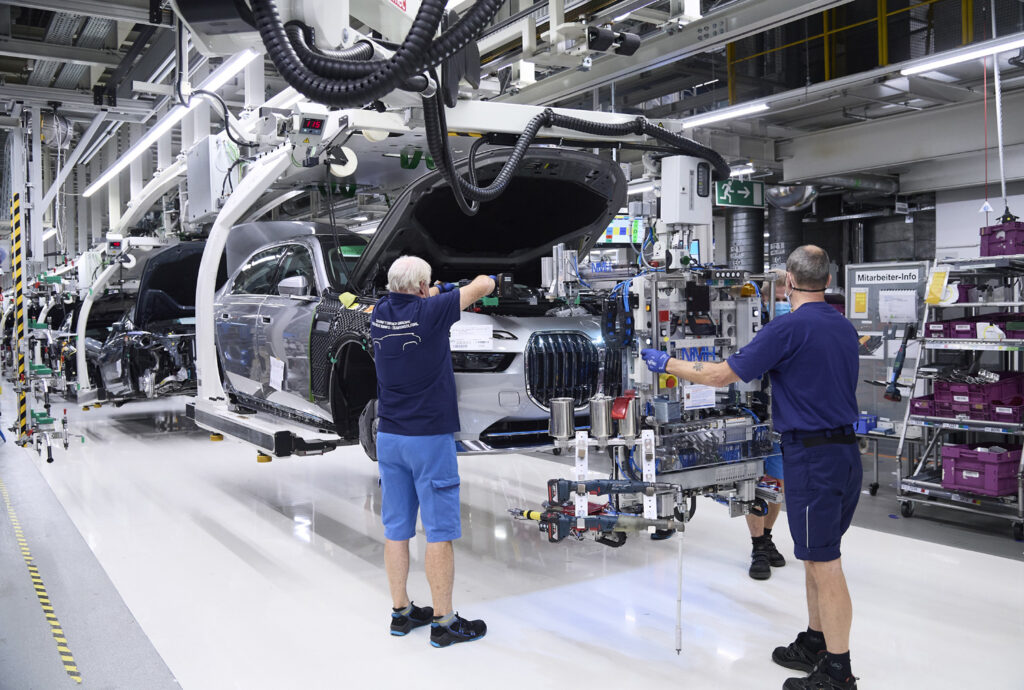
Încheiem vizita de la Dingolfing cu sentimentul că ne aflăm practic într-o plină perioadă de adaptare a uzinei la cele mai noi tehnologii, de la procesele noi din vopsitorie și până la inovațiile de pe liniile de asamblare.
Cu toate acestea, vorbim despre o uzină construită inițial în 1973, în plină criză a petrolului, care anul viitor va aniversa astfel 50 de ani de existență. Concepută pe baza unor procese și tehnologii care astăzi sunt evident depășite, uzina se adaptează în prezent la noile tendințe, însă acest proces este unul complex și plin de provocări logistice și tehnice.
Este și unul dintre motivele pentru care cea mai modernă uzină a Grupului BMW va fi, de fapt, cea care se construiește în prezent la Debrecen, în Ungaria, pe un teren cu o suprafață de 400 de hectare. De pe liniile de asamblare ale noii uzine vor ieși anual 150.000 de vehicule pentru care BMW promite zero emisii de dioxid de carbon în timpul producției. Producția este programată să înceapă în 2025, iar Debrecen va fi prima uzină a Grupului BMW unde se vor produce mașini electrice pe noua platformă Neue Klasse. Acolo, viitorul sună deja 100% electric.
Așa cum probabil îți imaginezi deja, noua uzină de la Debrecen va fi, de fapt, prima uzină a Grupului BMW concepută de la zero prin abordarea iFactory.
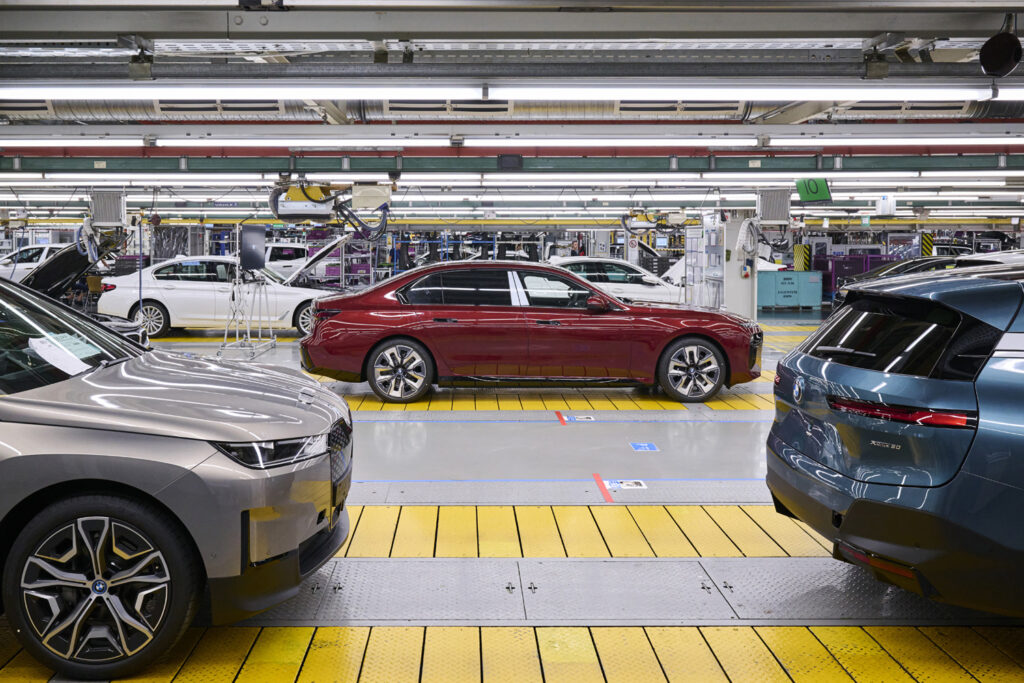