După cinci centre Continental deja vizitate, am început să diferențiez natura și activitatea centrului în funcție de primire. Să-ți explic: dacă ești întâmpinat cu rugămintea să te uiți dar să nu fotografiezi, atunci cel mai probabil ești într-un centru de cercetare și dezvoltare, acolo unde se fac operații deschise pe prototipuri sau dictări cu 1 și 0. Dacă ți se dă halat și ești încălțat cu botoși transparenți (cu fir de împământare chiar!), atunci urmează să vizitezi o linie de asamblare hi-tech, acolo unde iau naștere instrumentarele de bord digitale sau componente electronice sofisticate. Iar dacă primești niște bombeuri ca să-ți protejezi pantofii și, adiacent, degetele de la picioare, atunci probabil că ești într-un centru ContiTech, adică o linie de producție hardware din aia serioasă, unde se bate fierul cât e cald. Povestea care urmează este din aia cu bombeuri.
Mers fluid
În cazul platformei de producție ContiTech de lângă Timișoara, sintagma de mai sus este valabilă doar metaforic. Aici nu se lucrează cu fier, ci cu aluminiu și cauciuc. Și niciunul dintre materiale nu se bate, efectiv. Doar se îndoaie. Aici se fabrică MFS-uri (abr. eng.: mobile fluids systems), adică tubulatură pentru sisteme de răcire. În speță, cele de aer condiționat.
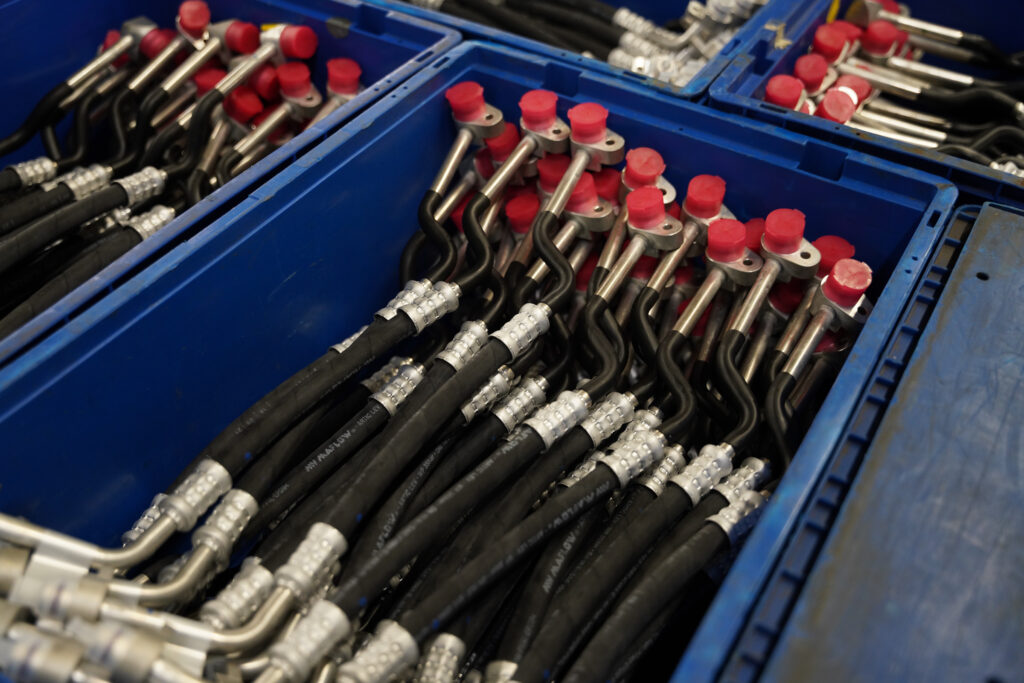
Țevile din aluminiu care ajung la Timișoara în formă brută sunt tăiate aici pe diferite lungimi, conform specificațiilor clienților. Apoi intră pe linia de producție, unde sunt prelucrate. Aluminiul este materialul preferat în ceastă zonă de producție mulțumită maleabilității sale. Ajutată de mașinării automatizate, țeava de aluminiu se contorsionează în orice formă cere marca auto care-o comandă, în principiu pentru că tubulatura aerului condiționat este ultimul element care trebuie să-și facă loc într-o mașină deja proiectată și trebuie să facă slalom printre celelalte piese; pe alocuri este și îmbrăcată în mănuși de cauciuc, pentru extra protecție la eventualul contact cu alte componente ale mașinii.
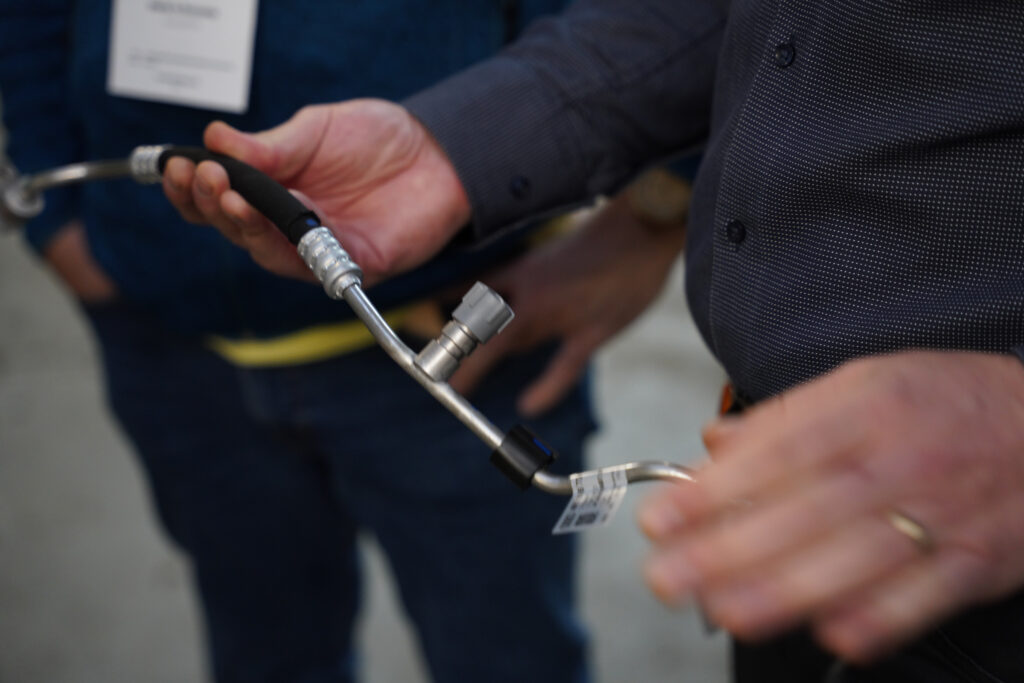
Platforma de producție are 20 de sisteme automatizate. Spre deosebire de centrele unde sunt produse componente hi-tech, unii roboții de aici sunt veterani – pentru că sisteme de aer condiționat se fac de mai demult decât instrumentarele de bord digitale. Însă chiar și aceștia au primit upgrade, fiind îmbunătățiți cu software și componente moderne. Trei dintre roboții de aici au primit software dezvoltat chiar în centrul Automotive din Timișoara.
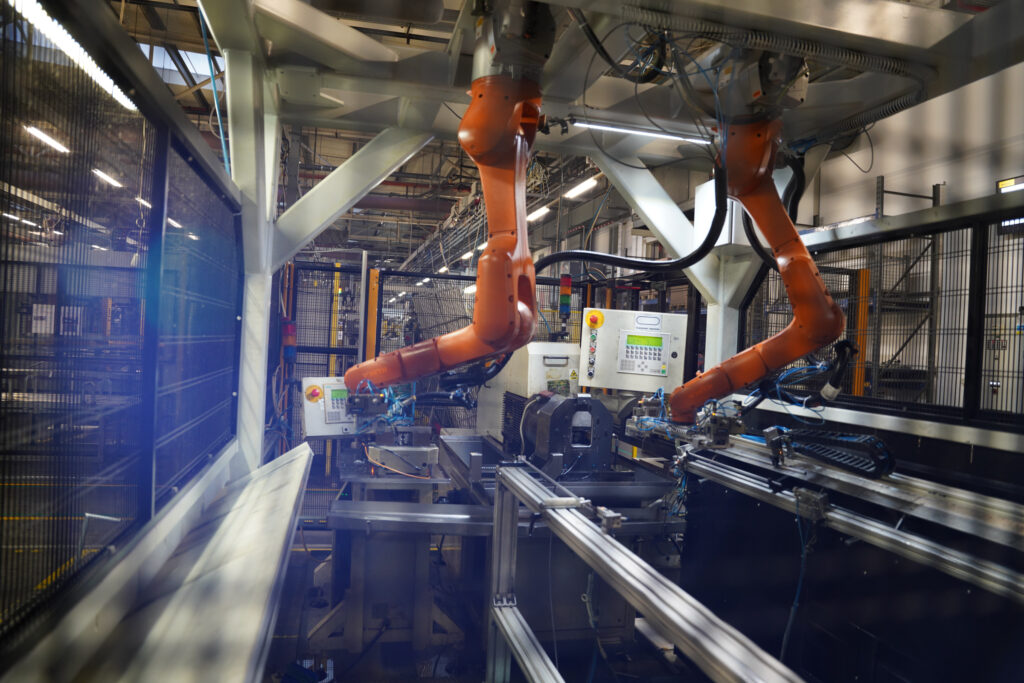
De aproape 20 de ani, de când această linie de producție a intrat în portofoliul Continental, roboții lucrează non-stop. Cot la cot cu ei, 1800 de muncitori își împart activitatea în trei schimburi; în oricare moment al zilei, 800 de repere (piese componente) sunt lucrate aici concomitent. La finalul unui ciclu de 24 de ore, peste 33000 de produse finite sunt împachetate și gata de livrare, nu înainte însă de a trece testul de etanșeitate. Nimic, nicio imperfecțiune nu le scapă angajaților de aici, iar produsul final trebuie să nu scape nici el nimic.
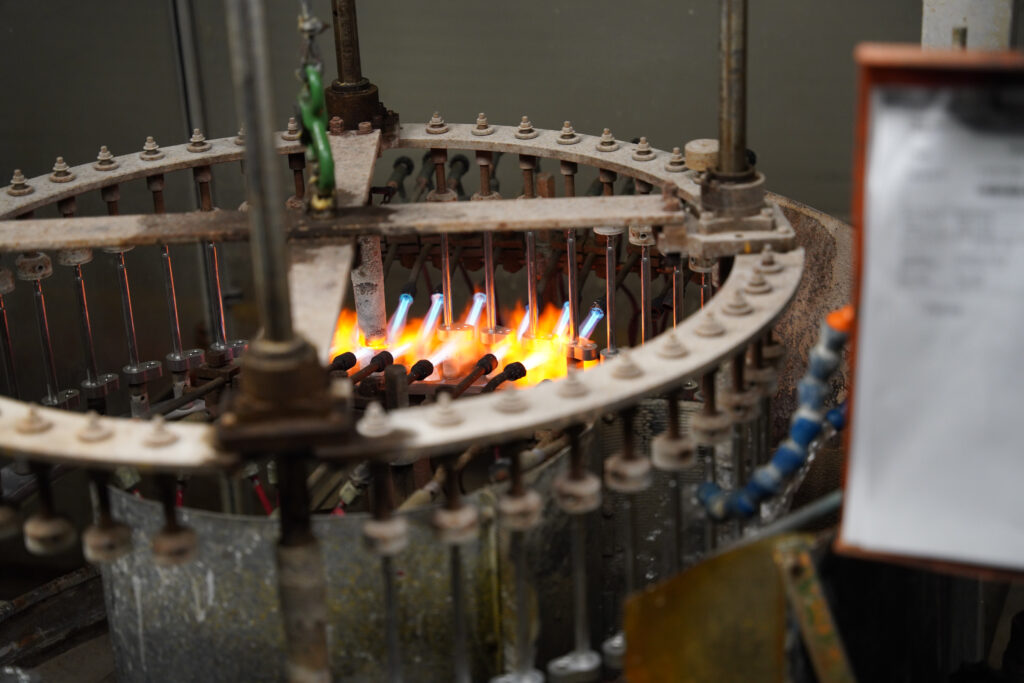
Am văzut fabrica de tubulatură de aer condiționat ContiTech de la Timișoara ca pe o exemplificare elocventă a evoluției industriale. Aici ești martor la tranziția dintre convențional și neo. Pe de o parte, aici găsești sisteme de lipire a metalului prin încălzire – elementele din aluminiu se unesc printr-un inel care se topește și le ține împreună. Apoi ajungi la aparatele laser, care fac același lucru în jumătate din timp, mult mai curat și cu emisii de agent termic considerabil mai mici. Sunt, deci, mai eficiente, mai curate și mai prietenoase cu mediul. În urma unei investiții de 2.1 milioane de euro începute în 2018, Continental a demarat aici tranziția către aparatura laser. Celor 10 unități laser deja existente li se vor mai alătura altele în următorii ani.
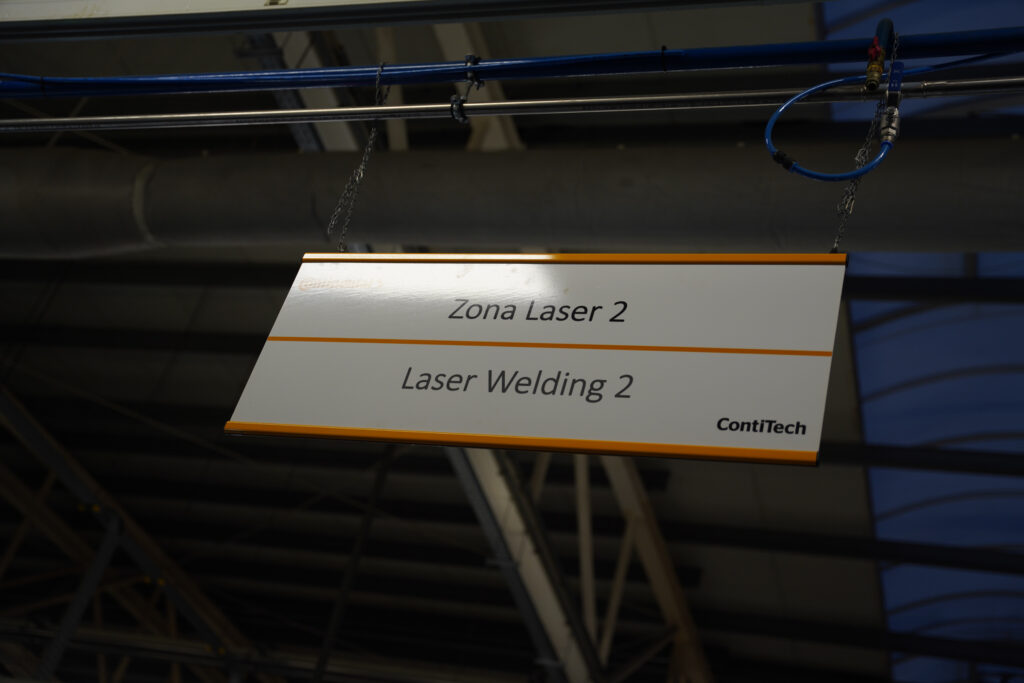
Alfa și Omega. Și din nou Alfa
După vizita platformei de producție, ceata de jurnaliști șleampeți – bombeurile de protecție pe care le montezi peste încălțările tale normale nu-ți modifică doar esteticul piciorului, ci și funcționalitatea lui, mai ales când ești obosit – formată din mine și colegii mei de presă auto a ajuns în locul în care ia naștere, conceptual, tubulatura de care v-am povestit mai sus: în departamentul de cercetare și dezvoltare MFS.
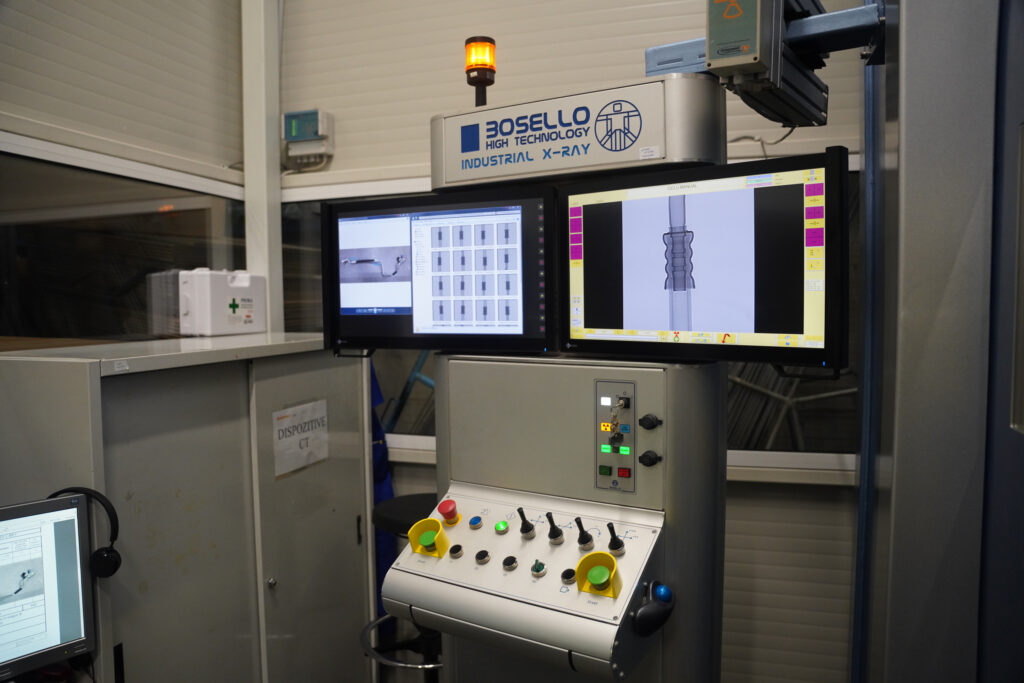
Departamentul a fost înființat în 2006 și este locul în care clienții (adică producătorii de mașini) sunt ajutați să-și materializeze proiectele. Pentru că unii dintre ei solicită consultanță în găsirea celei mai bune soluții (ca raport calitate/fiabilitate/preț). Alții știu foarte în detaliu ce vor și se prezintă cu un caiet de sarcini stufos, detaliat.
În acest moment, acesta este cel mai mare departament de cercetare și dezvoltare MFS al grupului Continental. Iar inginerii de aici ne-au spus că urmează să devină și mai mare – în cazul în care voiai să devii parte din familia Continental, informația asta poate e pont.
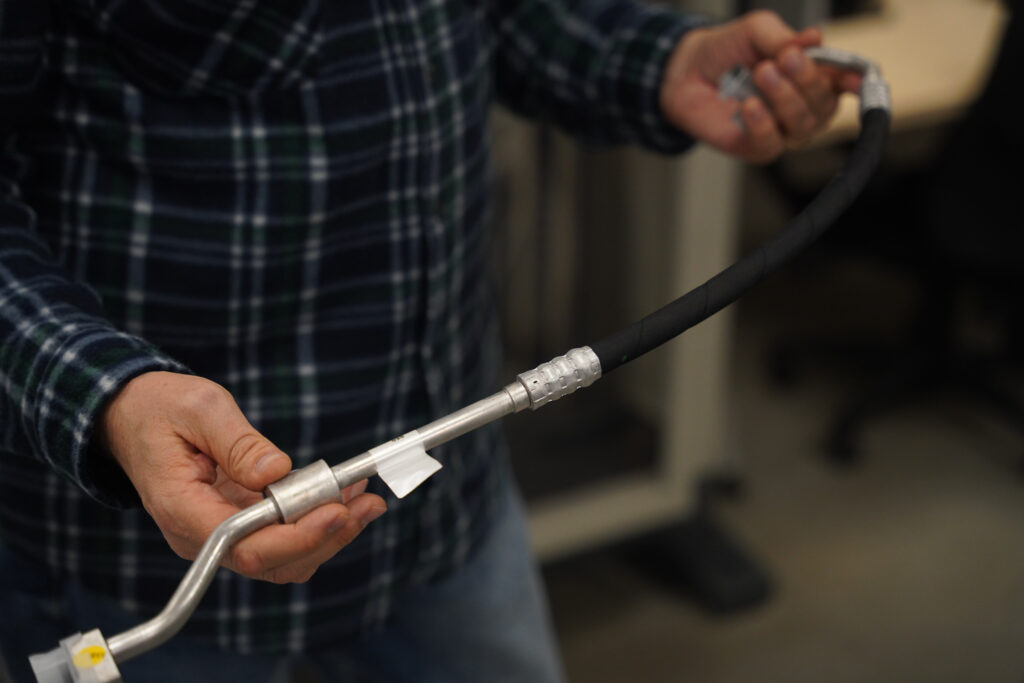
Ce trebuie să faci aici? Să creezi și să distrugi ca să poți mai apoi să creezi mai bine. Să mă explic: trebuie să testezi, de exemplu, rezistența și fiabilitatea sistemelor produse în fabrică. Ai aparate proiectate special ca să distrugă, de la menghină care trage de tubul de cauciuc pentru a testa rezistența îmbinărilor (s-a testat un furtun în fața noastră și am văzut cum oamenii ăștia calculează forțe, cupluri și timpi de parcă-s la Le Mans, nu lângă un aparat de la marginea Timișoarei). Am văzut și un aparat care „îmbătrânește” forțat un tub de cauciuc prin aplicarea de presiune constant, timp de două săptămâni, în reprize de 3 secunde, în interiorul său. Și mai ai și masă vibrantă, care, la fel, testează rezistența în timp a ansamblului.
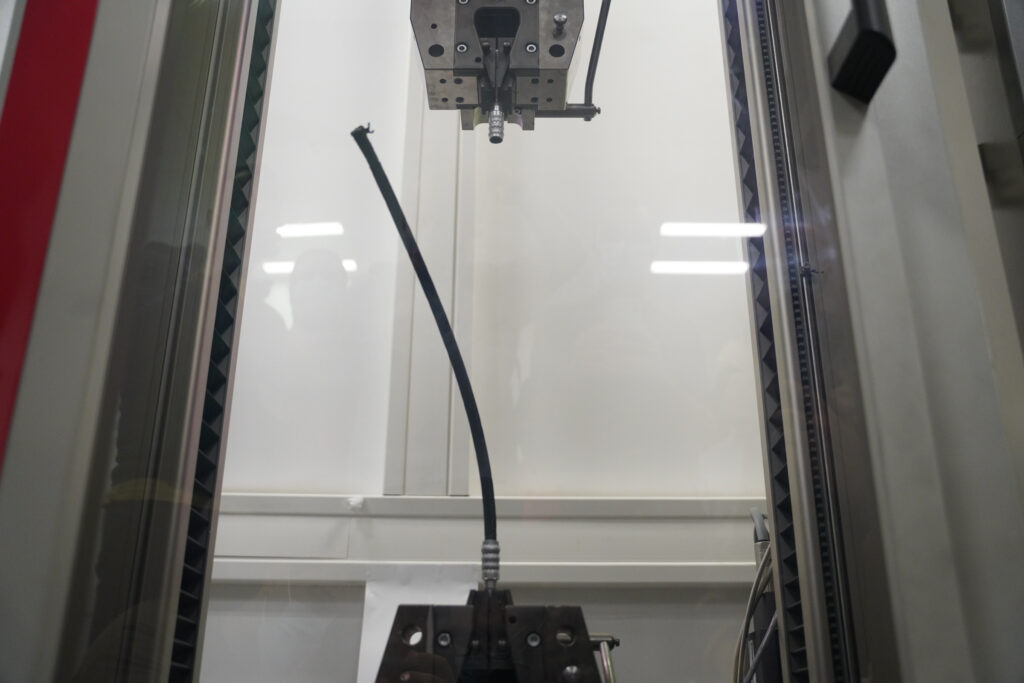
Sigur, toate acestea sunt făcute cu un rost științific: colectarea de date și prelucrarea lor în vederea îmbunătățirii soluțiilor tehnice. După cum ziceam: distrugi ca să poți crea. Ca să ai ce distruge. Și tot așa. În orice caz, de plictisit n-o să te plictisești. În plus, oamenii se pregătesc de mașinile electrice și de nevoile lor de răcire: deja se lucrează aici pe sisteme de răcorire a bateriilor.
Unicatele
Extinderea departamentului R&D a început deja și s-a materializat, printre altele, cu moștenirea unor mașinării din Germania. Mașinării cu care poți să produci prototipuri de sistem de tubulatură. Cu toate că tehnologia modernă face posibilă simulări foarte precise și în mediul virtual, anumite lucruri trebuie încercate live, iar atelierul de prototipuri va furniza departamentului de testare piesele cerute.
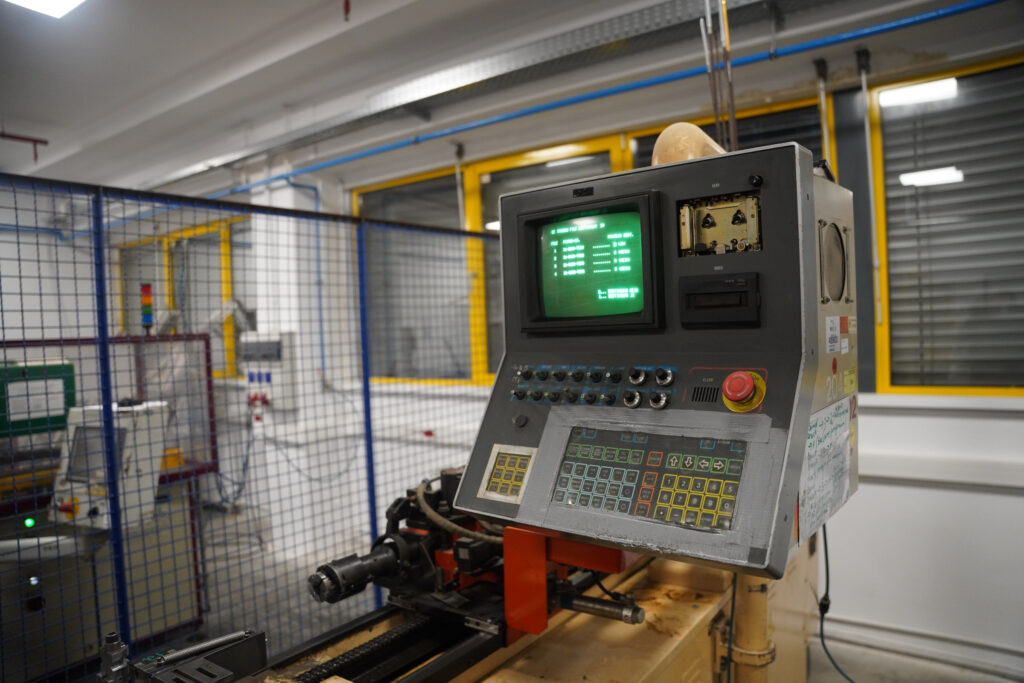
În plus, și clienții – fie noi, fie cei deja existenți – care aleg să se folosească de experiența Continental în dezvoltarea de sisteme MFS pot să comande prototipuri ale schițelor virtuale; prototipuri pe care să le poată testa la aparatele de care v-am povestit mai sus. Un beneficiu considerabil, având în vedere că noile aplicații precum sistemele de răcire a bateriilor mașinilor electrice sunt, deocamdată, teritoriu neexplorat complet. Multe vor fi de învățat și aici, mult mai multe probabil decât am învățat noi în vizitele noastre la centrele Continental.
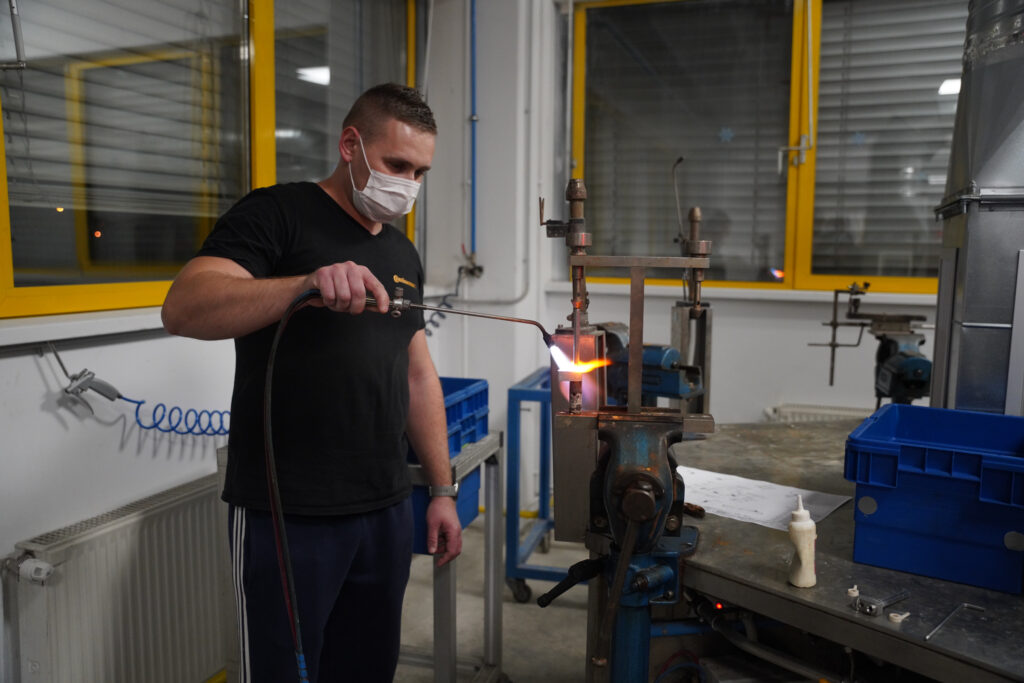
Am tot menționat „clienți” dar nu am spus și cine sunt: portofoliul de clienți ai fabricii de tubulatură de aer condiționat include Grupul Volkswagen, Grupul Renault-Nissan-Mitsubishi, Daimler, BMW, Volvo, Ford. Lista nu se încheie aici – aici mi s-a închis telefonul pe care am notat toată ziua informații, sătul probabil de notițele mele.
Cauciuc în buclă
Ansamblul de clădiri ContiTech Timișoara găzduiește și linia de producție de curele – atât cele de transmisie cât și cele de distribuție. Gazdele noastre de aici au fost succinte, pentru că producția unei curele „nu este atât de complicată”. Sau poate pentru că ne-au văzut fără vlagă și, la fel ca profii ăia cool de la școală, au scurtat ultimul curs ca să ne lase să plecăm mai repede.
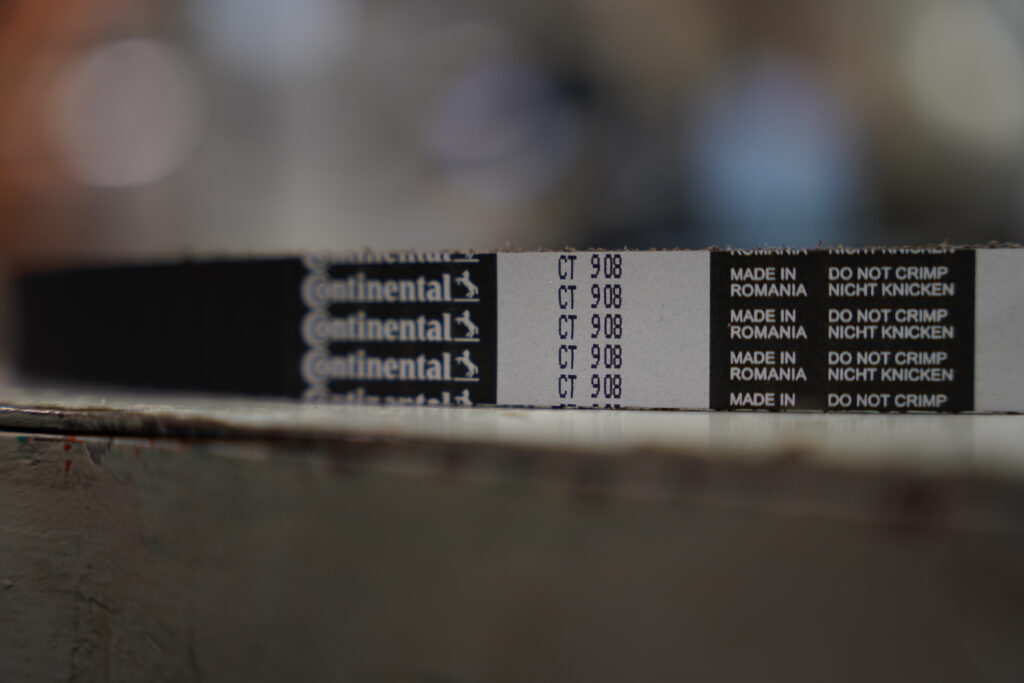
Sigur, nici nu este atât de simplă încât să poți să o faci acasă, pot să confirm asta. Sau, dacă reușești să o faci, atunci sigur nu poți să produci un milion și jumătate de curele pe lună, cât înregistrează acest departament. 50% dintre acestea sunt pentru piața aftermarket, cealaltă jumătate sunt comenzi OE (echipament original, parte din dotarea standard a unei mașini).
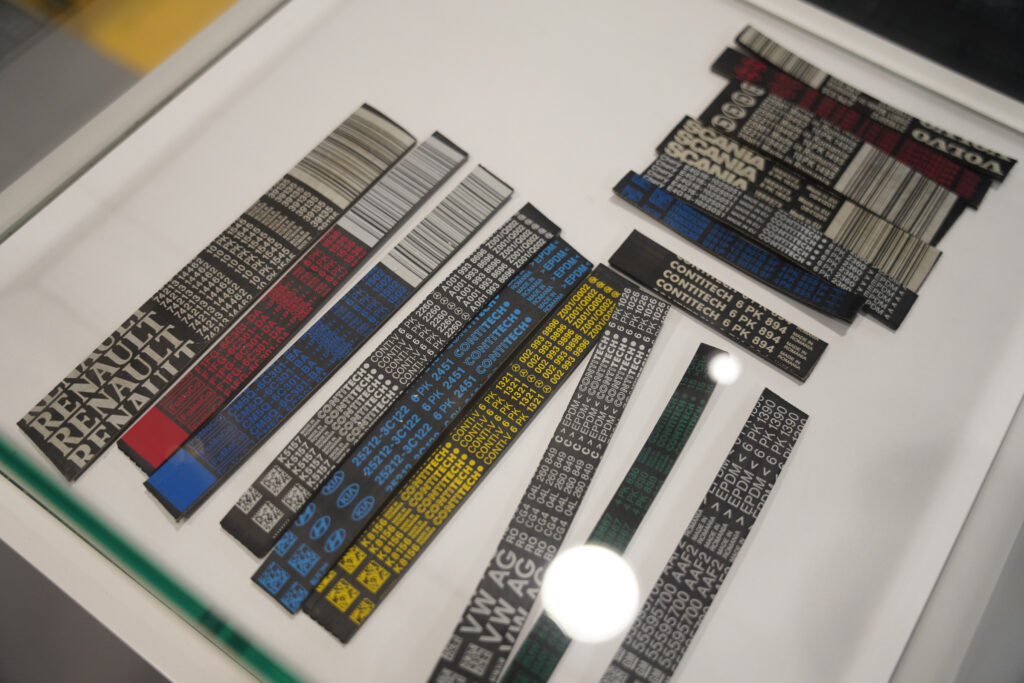
Cureaua intră pe linia de producție ca o placă de cauciuc, iar primul proces este confecționarea, adică transformarea unei limbi de cauciuc într-un cilindru de cauciuc. După ce se asigură îmbinarea perfectă a marginilor – că altfel fiecare ciclu de rotație al curelei ar fi semnalizat printr-o bătaie, adică prin zgomot –, rola de cauciuc primește un strat de material textil, care-i conferă textura poroasă. Dar, mai important, îi oferă extra silențiozitate și un coeficient sporit de frecare. Pasul trei este vulcanizarea, adică aplicarea canelurilor prin presare la cald. Procesul final este tăierea în fâșii. Et voilà!
Că tot am pomenit de profii cool din viața noastră: care cred eu că este secretul unui profesor de treabă? Pasiunea. Pasiunea aia care transpare, nu obsesia pentru materia lui.
Pasiune. Asta am văzut și în oamenii pe care i-am întâlnit în vizitele Continental. O dată a fost un inginer tânăr, care-mi vorbea despre robotul care asamblează instrumentare de bord. Altă dată, un supervizor de linie de producție care-și lăuda oamenii pentru capacitatea lor fizică și pentru precizie. Sau un inginer programator care-mi arăta cum a reușit să facă o suită de camere și senzori să vadă mai departe și mai bine decât celelalte suite de camere și senzori de până acum. Toți au avut datoria să ne explice și să ne arate ce anume lucrează, însă niciunul dintre ei n-a avut obligația să o facă zâmbind.
Și totuși.